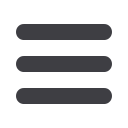

Technical article
March 2013
89
www.read-eurowire.com▲
▲
Figure 4
:
Nominal expansion rates
Wall (in.)
% volume air
Nominal expansion by wall thickness
Variation (6 SDEV)
Injector type
Nitrogen flow (cc/m in)
Actual capacitance (pf/ft)
Predicted capacitance
▲
▲
Figure 5
:
Gas flow and capacitance variation
as applicable. Typically the lower the melt
flow rate, the better the burn performance
(i.e. less smoke generation).
The higher the melt flow rate, the more
suitable the resin is for thinner insulation
walls and smaller cable designs.
Table 2
provides some general guidelines for resin
selection.
Process parameter
and effects – foam
expansion rates
It is common for cable engineers to
design cables using calculated expansion
rates yielding the lowest theoretical cost.
However, there are other important
factors that impact cost, such as process
ability, overall electrical performance and
cable damage and compression from
subsequent operations after extrusion.
Neglecting these design factors could
mistakenly result in higher cost and
significant scrap generation. Consider a
typical video coax cable designed using
a 59 per cent expansion rate versus the
same cable designed with a 54 per cent
expansion rate.
The cable with 59 per cent expansion
may push the process to its limits,
subsequently increasing start-up scrap
and causing greater process variation.
From an electrical standpoint, higher void
content typically results in larger cells and
higher formation of cells around the centre
conductor, which can have a major impact
on cable return loss.
Alternatively, the same cable can be made
at a 54 per cent expansion rate with a
weight increase of only 0.28lb/1,000ft.
This small change will provide a robust,
repeatable
product
with
improved
cable return loss, less scrap and higher
productivity with the same cable
impedance.
Figure 4
provides general
guidelines for foam expansion rates
based on the dielectric wall thickness.
Actual maximum expansion rates will vary
based on resin selection and processing
methods.
High-pressure nitrogen
gas injection
Foaming is achieved by injecting high-
pressure nitrogen gas into the molten
polymer during the extrusion process.
The rate of foaming is determined by the
flow rate of the gas in proportion to the
resin output at the operating RPMs of the
extruder. The higher the gas flow to the
resin output, the higher the expansion rate.
The consistency of this gas flow is critical
to maintaining a uniform expansion rate,
which is needed to maintain low variations
in cable capacitance and signal time delay
for the cable.
Measuring gas flow
Ensuring that a constant, correct gas flow
is injected into the melt is one of the most
important foaming process variables.
Undetected variation of gas flow will
result in capacitance variation, leading to
process instability and significant scrap.
Off-line injector flow measurements
(such as water displacement) will
determine the average injector flow rate
at room temperature. However, it will not
determine the actual process flow rate or
flow variation as injector flows can change
radically once heated to processing
temperatures.
Consequently, an in-line flow meter is
recommended when utilising the gas
injection foaming process. With a flow
meter, the gas pressure can accurately
be set to obtain the calculated flow
rate required for the desired nominal
capacitance. In addition, variations in flow
rate can be monitored.
Selecting the gas
injector for the product
When sizing an injector, the extruder
barrel pressure and the nitrogen flow rate
for the desired expansion rate versus the
product run speed need to be considered.
The flow rate of the gas is controlled by
the injector orifice size and the nitrogen
gas pressure. The orifice needs to be sized
so that the gas pressure is higher than
the barrel pressure for the desired gas
flow. Suppose a given cable construction
requires a flow rate of 50cc/minute of
nitrogen for a line speed of 600 feet per
minute and creates an extruder barrel
pressure of 1,000psig.
The selected injector for this process
needs to have the orifice sized no larger
than to deliver a gas flow rate of 50cc/
minute at pressure greater than the barrel
pressure.
With a flow rate greater than 50cc/minute
@1,000psig, the gas pressure would need
to be adjusted lower than the barrel
pressure and doing so would result in the
injector plugging leading to the product
going solid.