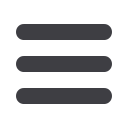

EuroWire – November 2008
71
technical article
The acrylategroups respondby crosslinking
via the freeradical mechanism of polymeri-
sation, following photo-initiation induced
by the UV curing lamps at draw. The
kinetics dictates a reduced cure speed
during processing, unless steps are taken
to modify the process for optimum cure.
This is achievable by an understanding of
the character of the primary coating curing
process.
There are at least two components of the
curing process that act to retard the rate of
polymerisation of the soft primary coating.
First, the high temperature of the curing
coatings induced by exposure to the high
intensity UV lamp environment and the
exotherm of polymerisation reactions
slows the overall observed rate
[8]
.
Second, it has been demonstrated that
close proximity of stacked UV lamps create
in effect rapidly superposed, repeated
photo-initiation periods. The rate of
disappearance of acrylate groups under
this condition is again retarded.
The disposition of UV lamps is such
that time is maximised between repeat
UV exposures resulting in a significant
increase in the coating degree of cure,
comparing processes with the same
speed and overall UV dose
[9], [10]
. Thus it is
possible to deal effectively with a reduced
modulus primary coating and achieve a
near-complete cure at required fibre draw
speeds.
A second aspect of the primary coating
for enhanced micro-bending protection
in FTTx applications is the temperature
dependence of the modulus. While a low
modulus may be a characteristic at room
temperature, deployment in the field will
find fibre exposed to temperature extremes
where microbend-inducing stresses may
be present. Therefore, a lowest possible
glass transition temperature T
g
is required
so that the primary coating remains soft
and protective in all situations.
A tough secondary coating is necessary
to protect the primary coating and glass
from damage during handling and
installation. This coating may be designed
to be inked as a colour code or it may be
colour-inclusive to provide identification
without the necessity of a separate inking
process.
3 Results
A new primary coating, a development
based on the commercial graded index
multi-mode product’s coating, has been
adapted for application to single mode
fibre
designs,
particularly
targeting
extreme deployment environments such
as FTTx.
The preferred secondary coating pro-
tecting the fibre structure features an
optimised colouring system inclusive in
the bulk, not requiring an extra layer of
ink to be added for colour-coding. The
new colours are enhanced for brightness
and visibility under dim lighting situations,
eg in deep shade or in manholes.
3.1 Mechanical properties
The dynamic mechanical properties of a
typical commercial primary coating are
shown in
Figure 2
.
The data was obtained on a TA DMA at
1 Hz oscillatory stress rate, taking care that
the strain is kept within the linear region of
stress-strain behaviour.
The sample of coating was cured on
polyester in a 75-micron film with a
UV dose of 1 J/cm
2
. The lamp used is a
mercury-halide bulb operating at 300 W/
inch output. This UV exposure is sufficient
to ensure the material is on the plateau
of the dose-modulus curve. The data
shows the equilibrium modulus to be
approximately 1.5 MPa.
On fibre, this coating typically cures well
to a modulus of about 0.8 MPa, a level
characteristic of most singlemode fibre
primary coatings in the industry. The
reasons for the discrepancy between the
film modulus and in-situ modulus are
detailed in references
[8]
through
[10]
.
The ‘T
g
’, estimated by the peak in tanδ, is at
approximately -30°C. Thus the coating, and
other similar formulations, will respond as
a glass at extreme low temperatures like
-40 to -50°C. (This is an incomplete picture,
as there is a time dependency to the stress
induced by strain at low temperature,
but the ‘T
g
’ remains a useful metric for
comparison).
Figure 3
shows the dynamic mechanical
properties of the new primary, using a
film sample made similarly to the above
example.
In
Figure 3
, the new primary coating
exhibits an equilibrium modulus at just
under 1 MPa in the cured film, and on fibre
the insitu modulus is typically measured at
0.3 to 0.4 MPa, the target.
Figure 2
▲
▲
:
Dynamic mechanical properties of a commercial singlemode primary coating, stress rate at 1 Hz
Figure 3
▲
▲
:
Dynamic mechanical properties of the new singlemode primary coating, stress rate at 1 Hz