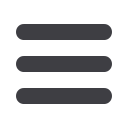

EuroWire – November 2008
72
technical article
With an eye to improving the low
temperature
protection
against
stress-induced micro-bending, the glass
transition temperature is shifted more
than 20°C lower than the typical coating
described in
Figure 2
.
A much more rapid relaxation of stresses
imposed during temperature excursions
is to be expected. The results of tests
designed to examine the micro-bending
protection are shown in the next section.
3.2 Micro-bending sensitivity
In order to establish a relative comparison
of microbend sensitivity between the
typical commercial primary coated fibre
and fibre with the new coating system,
two different methods were used for an
evaluation. Both methods are designed to
provide aggravated lateral stress conditions
(where the second method actually goes
well beyond what is normally encountered
in the field). After measuring the effect on
attenuation at room temperature, the test
structures can be temperature cycled to
determine the additional loss induced by
the temperature excursions.
The first test is a basketweave/temperature
cycling procedure. The sample fibre is
wound at 50 grams tension on a 300mm
diameter quartz cylinder with a 9mm
‘lay’. This creates numerous crossovers
fibre-to-fibre in the course of winding 50
layers on the drum.
The crossovers can cause added loss at
room temperature if the fibre is sensitive
enough, but normally little or no added
loss is seen at this point.
The drum with fibre on it is temperature
cycled, in this experiment through -40°C/
-60°C/+70°C/23°C two times while making
loss measurements at 1,550nm after one
hour at temperature through the cycles.
Figure 4
shows typical results for samples
of the new coating system versus samples
of a typical commercial system.
Both coating systems utilise coloured
secondaries, but different formulations
of secondary. The fibre specimens were
chosen to match coating geometry, mode
field diameter, and cut off wavelength.
The two different coating systems
both give good protection against the
micro-bending stresses at 23°C. At -40°C
the typical commercial primary is close
to its T
g
but still provides good protection
against micro-bending by stress relaxing in
a reasonable time frame.
Only a small added loss is seen at -40°C
in the typical primary and none in the
optimised primary fibre. At -60°C, the
optimised primary is likewise close to its T
g
,
with similar protection still provided, but
the typical primary is now well below T
g
and the fibres show added loss.
Desiring a more aggressive micro-bending
environment, for the second method the
IEC sandpaper drum test
[7]
was modified
to provide a harsh micro-bending stress
situation strong enough to affect single
mode fibre even at room temperature.
To do this, a 300mm diameter quartz
drum was wrapped with adhesive backed,
40 grit sandpaper, creating a very rough
surface around which a single layer of fibre
was wound at 100 grams tension.
Using matched fibre samples as with
the basketweave/temperature cycling test,
the 23°C attenuation was measured after
winding.
Then the drums were cycled to tempera-
ture extremes, this time measuring
attenuation at 1,550nm after one hour
and again after four hours at temperature.
The results are given in
Figure 5
.
The initial measurement at 23°C taken
while the fibre was on the original spools
shows similar loss of about 0.19 dB/km for
these fibre specimens.
After winding the drums, still at room
temperature, the lower modulus of the
optimised primary offers significantly
better protection than the typical primary,
with one third the added loss.
Throughout the very demanding range of
temperature and rough drum conditions,
the optimised coating fibre shows much
lower micro-bending response than the
typical commercial system.
Figure 4
▲
▲
:
Basketweave/temperature cycle results for typical commercial SM coating system (dashed) and the
optimised coating system (solid)
Figure 5
▲
▲
:
Sandpaper drum/temperature cycle results for typical commercial SM coating system (dashed) and the
optimised coating system (solid)