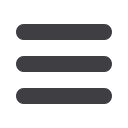

137
article technique
EuroWire – Mars 2009
De nombreux paramètres empiriques ont été
proposés pour compenser la consommation
incomplète des échantillons soumis à des
essais. Un de ces paramètres, connu comme
facteur fumée, a été récemment utilisé
avec des calorimètres mesurant le taux de
dégagement de la chaleur à petite échelle,
et associe les deux aspects cités plus haut:
l’occultation de la lumière et le taux de
dégagement de la chaleur.
La méthode d’essai la plus commune, à
petite échelle pour la mesure de la fumée
générée de la combustion de produits, est
la chambre à fumée NBS traditionnelle,
dans le mode vertical, conformément à la
norme ASTM E662. Étant donné le nombre
élevé de paramètres possibles en mesure
d’influencer la propagation de la combustion
et de la fumée, il n’est pas possible de
simuler un scénario d’incendie réel dans
la chambre à fumée NBS. Toutefois, il est
possible d’évaluer la génération de fumée
de différents composés dans des conditions
limites identiques. La norme ASTM exige des
mesures dans les deux modes: non-flambant
(échantillon fixé en position verticale
et exposé uniquement à une source de
chaleur radiante) et le mode flambant (avec
combustion à la base de l’échantillon).
La fumée ainsi générée réduit l’intensité d’un
rayon de lumière traversant la chambre en
direction verticale.
Toxicité
: Enfin, le danger d’incendie est
également associé, du moins dans une
certaine mesure, à la toxicité de la fumée
elle-même. La cause principale étant l’oxyde
de carbone (CO), le produit toxique le plus
important dans tout incendie, généré par
la totalité des matériaux organiques dans la
combustion. Durant la combustion le PVC,
par rapport à d’autres matériaux, dégage
une quantité de chlorure d’hydrogène et une
petite quantité de monoxyde de carbone.
Ces deux substances sont toxiques, mais avec
une différence fondamentale. Le chlorure
d’hydrogène est immédiatement perceptible
et irritant, et dégage une odeur âcre qui
stimule les personnes à abandonner la zone
concernée. En outre, cet acide se dépose sur
les parois et disparaît rapidement de la masse
gazeuse. L’oxyde de carbone, par contre,
est inodore et sans saveur et s’accumule
dans une concentration suffisante à causer
une perte de conscience avant l’évacuation
de la zone concernée. C’est l’oxyde de
carbone, avec la chaleur et la fumée qui se
développe avec la combustion des matériaux
organiques, le principal responsable des
décès durant les incendies: il est connu
comme “l’assassin silencieux”.
En ce qui concerne le risque de formation de
dioxines (normalement liée à la combustion
incontrôlée
des
matériaux
contenant
le chlore), plusieurs études ont mis en
évidence que les quantités émises durant
un incendie accidentel sont négligeables: Il
n’y a aucune augmentation appréciable du
niveau général des dioxines présentes dans
l’atmosphère (les niveaux sont inférieurs
à 0,1%). Par conséquent, il n’existe aucun
risque supplémentaire pour les personnes
ou pour l’atmosphère dans le cas d’incendie
entraînant des quantités élevées de PVC.
2 Les composés de PVC:
une contribution à la
soutenabilité
La tendance des ces dernières années
consiste à éliminer les risques pour
l’environnement et pour la santé humaine.
La directive RoHS (2002/95 EC) réglemente
la “restriction de l’utilisation de certaines
substances
dangereuses
dans
les
équipements électriques et électroniques”.
Cette directive bannit l’introduction sur
le marché de nouveaux équipements
électriques et électroniques ayant une teneur
trop élevée en plomb, cadmium, mercure,
chrome hexavalent, et des retardeurs de
flamme bromés (les biphényles polybromés
ou PBB) et les diphéniléthers polybromés
(PBDE).
Il ne s’agit que du premier pas vers la
production
de
matériaux
respectant
l’environnement.
Le Règlement REACH EC 1907/2006 relatif à
l’Enregistrement, l’Évaluation, l’Autorisation
et la Restriction des produits chimiques
(Registration Evaluation and Authorisation
of Chemicals) est entré en vigueur le 1er
juin 2007, dans le but d’augmenter le niveau
de protection de la santé humaine et de
l’atmosphère. Ce règlement comprenait
également la promotion de méthodes
alternatives pour l’évaluation des dangers
inhérents aux produits chimiques ainsi que la
libre circulation de substances dans l’ UE, en
renforçant en même temps la compétitivité
et l’innovation.
Les priorités du règlement REACH sont les
suivantes:
L’enregistrement d’environ 30 000 substances,
commercialisées et produites avant 1981
ou importées en quantités d’1 tonne par
an; en définissant le principe OSOR (one
substance, one registration) “une substance,
un enregistrement” visant à invertir la
soi-disant charge de la preuve, en imposant
aux producteurs ou aux importateurs de
démontrer que la commercialisation de
leur produits chimiques peut avoir lieu
sans entraîner aucun danger pour la santé
humaine et pour l’environnement.
Autorisation et remplacement des
•
substances dangereuses, en s’assurant
que les risques sont contrôlés de façon
appropriée et que ces substances sont
remplacées par des substances ou des
technologies appropriées
Obligation de diligence de la part des
•
fabricants, des importateurs et des
utilisateurs
Restrictions
dans
les
applications
•
spécifiques
Haut niveau de protection de la santé
•
humaine et de l’environnement en cas
d’utilisation de produits chimiques
Communication des informations et
•
partage des données selon le principe
“no data, no market” (“pas de données,
pas de marché”)
Grâce à sa versatilité dans plusieurs
applications et aux coûts compétitifs, le PVC
est toujours un matériau d’élection pour
l’industrie du bâtiment ainsi que pour les
outillages et les équipements du secteur
médical, et ce dès son apparition à grande
échelle au début des années ’50.
Au cours de cette dernière décennie, les
méthodes de fabrication des résines et les
caractéristiques des stabilisateurs ont subi
un changement énorme dû aux restrictions
des règlements en matière de substances
dangereuses, et aux efforts visant à obtenir
des matériaux recyclables et conformes aux
exigences de soutenabilité.
Les stabilisateurs du PVC ont été longuement
examinés et la préoccupation majeure
concerne les produits contenant des métaux
lourds. Par conséquent, nombreuses sont
les restrictions imposées par l’industrie,
par les règlements gouvernementaux et
par les utilisateurs du PVC. Un exemple de
la versatilité du PVC est représenté par le
remplacement des stabilisateurs à base de
plomb avec d’autres systèmes sans métaux
lourds tels que les stabilisateurs à base de
Ba-Zn, Ca-Zn et Al/Mg/Ca/Zn.
3 Objectifs pour le
développement
des composés FREC
(Flame Retardant
Eco Compounds)
Le projet de B & B Compounds visait à
développer une nouvelle gamme de
composés de PVC éco-compatibles et
ignifuges. Il existe plusieurs options tech-
nologiques disponibles pour remplacer les
stabilisateurs à base de métaux lourds et
le Sb
2
O
3
.
3.1 La fonction des stabilisateurs dans le PVC
Lorsque le PVC est traité à des températures
élevées, il se dégrade par déshydrochloration,
par scission de chaîne et par réticulation de
macromolécules. Le chlorure d’hydrogène
(HCL) libre se dégage en entraînant la
décoloration de la résine ainsi que des
changements des propriétés physiques
et chimiques significatifs. Le dégagement
de HCL a lieu par élimination de la chaîne
du polymère; la décoloration est due à
la formation de séquences de polyènes
conjugués de 5 à 30 doubles liens (réaction
primaire).
Les réactions successives de polyènes
conjugués hautement réactifs causent
la réticulation ou la scission de la chaîne
polymérique, et forment du benzène et des
traces minimales de benzène condensé