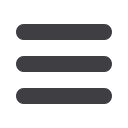

EuroWire – Mars 2009
138
article technique
et/ou alcalinisé en fonction de la tempéra-
ture et de l’oxygène disponible (réactions
secondaires).
La dégradation doit être contrôlée par
l’addition de stabilisateurs. Le stabilisateur
de chaleur doit éviter la réaction de
déshydrochloration, qui est le processus
primaire de dégradation.
Les systèmes calcium-zinc représentent une
alternative satisfaisante aux stabilisateurs
à base de plomb, comme récemment
démontré par son utilisation croissante.
Les principaux secteurs d’application des
systèmes Ca-Zn sont les secteurs du fil et du
câble et le secteur des finitions intérieures
des voitures, suivis des tuyaux et des profils.
Les
composés
métalliques
ont
été
sélectionnés comme stabilisateurs sans
plomb puisque leur effet sur le corps humain
est négligeable, et donc leur probabilité
d’être sujets à des règlements et à des
restrictions dans le futur est minimale.
En associant les stabilisateurs obtenus de
ces métaux, une résine à base de PVC a été
développée avec un stabilisateur sans plomb
indiquée pour l’utilisation dans les isolements
et les revêtements de fils.
3.2 La fonction des retardeurs de
flamme dans le PVC
Le processus de combustion peut être
synthétisé dans les phases suivantes:
Réchauffage
•
Décomposition (pyrolyse)
•
Allumage et combustion
•
Propagation avec retour thermique
•
Le réchauffage du matériau moyennant des
sources thermiques extérieures augmente
la température du matériau à une vitesse
qui dépend de l’intensité de la chaleur
émise, des caractéristiques de conductivité
thermique du matériau, de la chaleur latente
de fusion et de vaporisation et de la chaleur
de décomposition.
Après avoir atteint une température
suffisante, le matériau commence à se
dégrader en formant des mélanges gazeux
et liquides. Ces mélanges se forment à une
vitesse qui est fonction de l’intensité de
réchauffage du matériau polymérique.
La
concentration
des
produits
en
décomposition, en se mélangeant avec
l’air environnant, augmente jusqu’à rentrer
dans l’intervalle d’inflammabilité. Dans
cette situation, la présence d’une source de
chaleur cause l’allumage du mélange. La
chaleur générée est partiellement irradiée
au matériau (retour thermique) de façon à
poursuivre avec la pyrolyse.
L’action d’un retardeur de flamme consiste
à éliminer ou à limiter un des facteurs, en
agissant physiquement ou chimiquement
(ou des deux façons) sur les produits liquides,
solides et gazeux se formant durant le
processus.
L’action physique est de trois types:
Refroidissement du processus de retour
•
thermique, qui arrête la fourniture de
la chaleur nécessaire à poursuivre la
pyrolyse du matériau polymérique
Dilution du mélange de combustion
•
Formation d’une couche de protection,
•
où le matériau polymérique solide est
protégé avec l’oxygène provenant de la
phase gazeuse riche, au moyen d’une
couche de protection solide ou gazeuse.
L’on obtient ainsi une réduction de
la chaleur irradiée au polymère, d’où
un ralentissement de la pyrolyse, et
réduction de l’apport d’oxygène au
processus de combustion
L’action chimique peut se dérouler comme
suit:
Réaction en phase gazeuse: Les radicaux
•
sont générés chimiquement par le
retardeur de flamme pour agir sur le
processus de combustion
La réaction en phase gazeuse condensée
•
peut avoir lieu en deux modalités
différentes. La première consiste en la
formation d’une couche de protection
de carbone (résidu charbonneux) sur
la surface du polymère, présentant les
caractéristiques d’un isolant thermique
et faisant fonction de barrière entre les
produits de la pyrolyse et l’oxygène
La seconde consiste en l’augmentation
de cette couche entraînant le retard du
processus de retour thermique.
Les retardeurs de flamme additionnés au
matériau peuvent être de types différents:
Réactif: réagit chimiquement avec le
•
polymère
Additif: mélangé au polymère
•
Réactif et additif: présent dans le
•
matériau sous les deux formes
Le choix du retardeur de flamme est influencé
par les facteurs suivants:
Toxicité
•
Biodégradabilité
•
Stabilité de la chaleur dans le polymère
•
Le
trioxyde
d’antimoine
(Sb
2
O
3
)
est
normalement additionné afin de réduire
l’inflammabilité du PVC plastifié; toutefois
cette substance permet également d’arrêter
plus efficacement le mécanisme de la chaîne
des radicaux en phase gazeuse, mais il
augmente la quantité de fumée générée en
cas d’incendie.
De nombreuses sociétés spécialisées dans le
traitement du PVC ont manifesté leur intérêt
pour d’autres additifs retardeurs de flamme
alternatifs permettant une réduction de
l’inflammabilité sans entraîner la production
de composants toxiques ou corrosifs. Le
retardeur de flamme ne devrait pas influencer
négativement les caractéristiques spécifiques
du PVC.
En outre, il est à souhaiter que toute
amélioration de la capacité de résistance à
la flamme soit associée à une réduction de
la densité des fumées. En cas d’ incendie, le
PVC dégage du chlorure d’hydrogène (HCl),
avec l’humidité toujours présente dans
l’air. Normalement l’on utilise le carbonate
de calcium dans le PVC comme agent
d’épuration de l’acide et charge économique.
En définitive, un retardeur de flamme idéal
devrait présenter également ces avantages
3.3 Étude concernant la possibilité
d’incorporer les nanofillers dans
le PVC
Récemment, les nanocomposites poly-
mériques (PNC), et notamment les nano-
composites polymère/argile, ont suscité un
intérêt considérable. Trois différents types
de nanocomposites peuvent être obtenus
lorsqu’un silicate stratifié est dispersé dans
une matrice polymérique. Cela dépend de
la nature des composants utilisés tels que
la matrice polymérique, le silicate stratifié
et le cation organique. Si le polymère ne
réussit pas à s’intercaler entre les lamelles de
silicate, l’on obtient un microcomposite. Ce
composite à phases séparées présente les
mêmes propriétés que les microcomposites
traditionnels.
Outre cette famille classique de composites
à base de polymère-charge, l’on peut obtenir
deux types de nanocomposites:
Structures
intercalées
se
formant
•
lorsqu’une ou plusieurs chaînes poly-
mériques étendues sont intercalées
(interposées) avec des couches de
silicate
Réactions en chaîne
(“mécanisme zip”)
HCI
PVC
HCI
Cycle de combustion du polymère
▲
▲
Intercalés
(nanocomposites)
Exfoliés
(nanocomposites)
Phases séparées
(microcomposites)
Silicate stratifié Polymère
Diagramme illustrant trois types principaux de
▲
▲
nanocomposites pouvant être obtenus lorsqu’un
silicate stratifié est dispersé dans une matrice
polymérique
Substances
volatiles
oxygène
Flamme
Produits
Chaleur
Polymère
Cycle de
combustion du
polymère
Dispersion
Phase
gazeuse
Résidu charbonneux
Phase
condensée