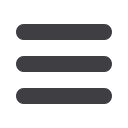

EuroWire – Marzo de 2009
151
artículo técnico
El método de prueba más corriente a
pequeña escala para medir el humo de
productos combustibles es la cámara de
densidad óptica vertical de humo (definida
por la NBS), según la norma ASTM E662.
Debido al gran número de parámetros
posibles que influencian la propagación
de la combustión y del humo, no es posible
simular lo que sucede en un incendio real
con una cámara NBS. Sin embargo, es
posible evaluar la producción de humo de
varias formulaciones en condiciones límite
idénticas. La norma ASTM exige mediciones
ya sea con el modo sin llama (la muestra,
montada en posición vertical, está sometida
solamente a la fuente radiante de calor)
ya sea con el modo con llama (llamas en la
parte baja de la muestra). El humo producido
reduce la intensidad de un rayo de luz que
atraviesa verticalmente la cámara.
Toxicidad
Por último, los peligros causados por un
incendio están asociados también, por lo
menos en cierta medida, a la toxicidad del
humo. La razón principal es que el producto
tóxico más importante en cualquier incendio
es el monóxido de carbono (CO) producido
por la combustión de todos los materiales
orgánicos. Durante la combustión, el PVC,
respecto a otro materiales, emite más ácido
clorhídrico y poco monóxido de carbono.
Estos dos gases son tóxicos, pero con una
diferencia sustancial. El ácido clorhídrico
es inmediatamente perceptible e irritante,
con un olor acre que obliga a dejar el área
afectada. Además, se deposita en las paredes,
desapareciendo rápidamente de la masa
gaseosa. En cambio, el monóxido de carbono
es inodoro e insípido, y aumenta hasta tales
concentraciones que puede causar pérdida
de conocimiento antes de la evacuación del
área. Es el monóxido de carbono, además
del calor y del humo que se desarrollan
con la combustión de todos los materiales
orgánicos, el responsable de las muertes
en los incendios: es llamado “el asesino
silencioso”.
Por lo que se refiere al riesgo de formación
de dioxinas (normalmente relacionada con
la combustión incontrolada de materiales
que contienen cloro), varios estudios han
revelado que las cantidades emitidas durante
un incendio accidental son muy bajas: no
hay un aumento apreciable del nivel general
de dioxinas presentes en la atmósfera (los
niveles son inferiores a un 0,1%). Por lo tanto,
el riesgo no es mayor para las personas o
el ambiente en caso de un incendio con
grandes cantidades de PVC.
2 Los compuestos de
PVC: un aporte a la
sostenibilidad
La tendencia de los últimos años es eliminar
los riesgos para el medio ambiente y la
salud humana.
La directiva conocida como RoHS (2002/95
EC) regula la “restricción a la utilización
de determinadas sustancias peligrosas en
aparatos eléctricos y electrónicos”. Esta
directiva prohíbe la comercialización en el
mercado EU de nuevos aparatos eléctricos y
electrónicos con niveles de plomo, mercurio,
cadmio,
cromo
hexavalente,
bifenilos
policromados (PBB) y retardantes de la llama
de éter de bifenilo policromado (PBDE)
mayores de los permitidos.
Esto es sólo uno de los pasos para llegar a la
producción de materiales que respecten el
ambiente.
El reglamento EC 1907/2006 REACH
(Registration Evaluation and Authorisation
of Chemicals) sobre registro, evaluación,
autorización y restricción de sustancias y
preparados químicos, fue adoptado el 1
de junio de 2007 para aumentar el nivel
de protección de la salud humana y de
la atmósfera. Incluía la promoción de
varios métodos para evaluar los peligros
de sustancias y preparados químicos,
además de su libre circulación en el
mercado EU, reforzando al mismo tiempo la
competitividad y la innovación.
Las prioridades del reglamento REACH son:
El registro de aproximadamente 30.000
•
sustancias, comercializadas antes de 1981
y producidas o importadas en cantidades
de 1 tonelada al año; este registro seguirá
el principio OSOR (One Substance,
One Registration) de “una sustancia,
un registro”, para invertir la carga de la
prueba y obligar a los productores o a
los importadores que demuestren que
la comercialización de sus productos
químicos no supone un peligro para la
salud humana ni para el ambiente.
Autorización y sustitución de sustancias
•
peligrosas, asegurándose de que los
riesgos sean controlados adecuadamente
y
que
dichas
sustancias
sean
reemplazadas por sustancias adecuadas
o alternativas tecnológicas.
Cumplimiento de las normas vigentes
•
por parte de fabricantes, importadores y
usuarios de sustancias.
Restricciones en aplicaciones específicas.
•
Alto nivel de protección de la salud
•
humana y del medio ambiente en caso
de uso de productos químicos.
Comunicación y condivisión de los datos
•
según el principio “no data, no market”
que prevé la obligación de pre-registro
(si la sustancia no es registrada no puede
ser comercializada).
Gracias a su versatilidad en las aplicaciones
y sus costos competitivos, el PVC representa
un material preferido en el sector de
la construcción, como también para
componentes y equipos en el campo médico,
desde su aparición a gran escala a inicios de
los años cincuenta.
Los métodos de fabricación de las resinas
y las características de los estabilizadores
han experimentado un enorme cambio
durante los últimos diez años, debido a
las restricciones normativas en materia de
sustancias peligrosas, y a los esfuerzos para
obtener materiales reciclables y conformes a
los requisitos de sostenibilidad.
Los estabilizadores para PVC han sido
examinados atentamente durante tiempo
y la preocupación principal se centra en los
productos que contienen metales pesados.
Como resultado, hay muchas restricciones
impuestas por la industria misma, los
reglamentos gubernativos y los usuarios del
PVC.
Un ejemplo de la versatilidad del PVC
es la sustitución de estabilizadores de
plomo con otros sistemas sin metales
pesados como los estabilizadores de Ba-Zn,
Ca-Zn y Al/Mg/Ca/Zn.
3 Objetivos para
el desarrollo de
productos FREC
(Flame Retardant
Eco Compounds)
El proyecto de B & B Compounds se
centra en el desarrollo de una nueva
gama de compuestos eco-compatibles
retardantes de la llama. Hay varias opciones
tecnológicas disponibles para reemplazar los
estabilizadores a base de metales pesados y
el Sb
2
O
3
.
3.1 La función de los estabilizadores en
el PVC
Cuando se elabora el PVC a altas
temperaturas,
éste
se
degrada
por
dehidroclorinación, escisión de cadenas
y reticulación de las macromoléculas. Se
genera cloruro de hidrógeno libre y tiene
lugar la decoloración de la resina, junto con
cambios importantes de las propiedades
físicas y químicas. La liberación del HCI tiene
lugar por eliminación a partir del esqueleto
principal del polímero; la decoloración es
debida a la formación de secuencias de
polienos conjugados con entre 5 y 30 dobles
enlaces (reacciones primarias).
Las reacciones siguientes de polienos
conjugados altamente reactivos causan
la reticulación o la escisión de la cadena
polimérica, y forman benceno y cantidades
mínimas de bencenos condensados y/o
alcalinizados según la temperatura y el
oxígeno disponible (reacciones secundarias).
La degradación debe ser controlada
agregando estabilizadores. El estabilizador
de calor debe evitar la reacción de
dehidroclorinación que es el proceso
primario de la degradación.
Reacciones en cadena
(“mecanismo zip”)
HCI
PVC
HCI