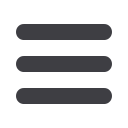

13
History of the Toyota Production System
In 1929, the Toyoda family sold the patent for weaving looms to England and
decided to produce cars. By 1950, they were studying the production systems in General
Motors (GM) and FORD plants in the USA. Because of the market conditions on the
Japanese islands, which were totally different from the automotive market in the USA,
they had to develop a production system able to efficiently produce small production
volumes of different variants of cars. After 40 years, Toyota has developed the Toyota
Production System able to produce the same amount of cars with half the number of
people and 50% better quality than its main competitors (see Figure 1.4).
Figure 1.4 Development of TPS success
The success of TPS was not only in the economy and family classes but even
among luxury brands, where Toyota Lexus surpassed the traditionally luxury brands
like Mercedes, BMW and AUDI in the USA in the late 1990s. In 2008, Toyota became
number 1 in terms of volumes sold in the world after 40 years of domination by GM.
Seven kinds of waste in logistics
Logistics processes are responsible for interactions in the supply chain. However,
lean improvements have been focused so far on production added value and waste.
Logistics places the same importance on added value and waste. The availability of all
resources is an inseparable part of the value-added activities because logistics added
value reflects the new reality of the worldwide markets. Flexibility and availability
enabling satisfaction of customer wishes do not have such an importance in the past
either for producers or for customers [30]. Classical “lean books” describe 7 wastes
in production. Nevertheless, 7 wastes in logistics have the same importance [56].
Supply chain activities responsible for flow contain a huge amount of waste during the
information flow of the order or the physical flow of the product. The success of the
interactions between production chains in the supply chain is critically dependent on
the identification of waste in logistics caused by delivering a product before it is needed,
delays during manipulation and delivery flow as well as unutilised and unnecessary
transportation, motion, inventory, space and errors.