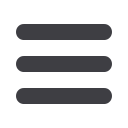

16
difference between mass and lean is the understanding how to increase the productivity.
Meanwhile, mass production focuses on the “producing more” principle to reach
minimum unit costs (production value added) through the economies of scale. Lean
production focuses on the “consuming less” principle observing the reduction of the
total costs (production, logistics value added and production, logistics waste).
Standard cost accounting leads to minimisation of unit costs of particular chains
in the supply chain. Concrete goals of the chains in the supply chain are then set based
on the sum of costs and goals of the related cost centres rather than as a reflection of
customer requirements. Today, cost accounting is in this matter more anti-lean as it is
incapable of identifying positive effects of lean such as productivity growth and cost
reduction (see Figure 1.7).
Figure 1.7 Differences in cost allocation in mass and lean [31]
The inaccurate perception of productivity, explained in the previous paragraph,
considers as productive whatever is produced rather than only what is demanded, which
causes a highly inaccurate allocation of costs. Lean SCM involves a system view so its
aim is to reduce the cost of the complex. Therefore, activities causing waste have the
same importance as those adding value. The benefits of lean could only be made visible
when the cost of wasting is identified and calculated (see Figure 1.7, lean SCM – batch
production). Unit cost of wasting has to be considered in today’s cost accounting so that
the waste could be made visible [31].
The previous three changes require the new attitude to management of supply
chains. Functional management is focused on insular optimisation of single departments
or chains. On the other hand, process management enables optimisation of total affects
which are also dependent not only on cost accounting of performances of related
departments but also on evaluation of productivity and the capacity of optimisation
itself. Management of the particular parts built on planning, organising and control