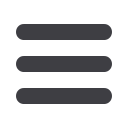
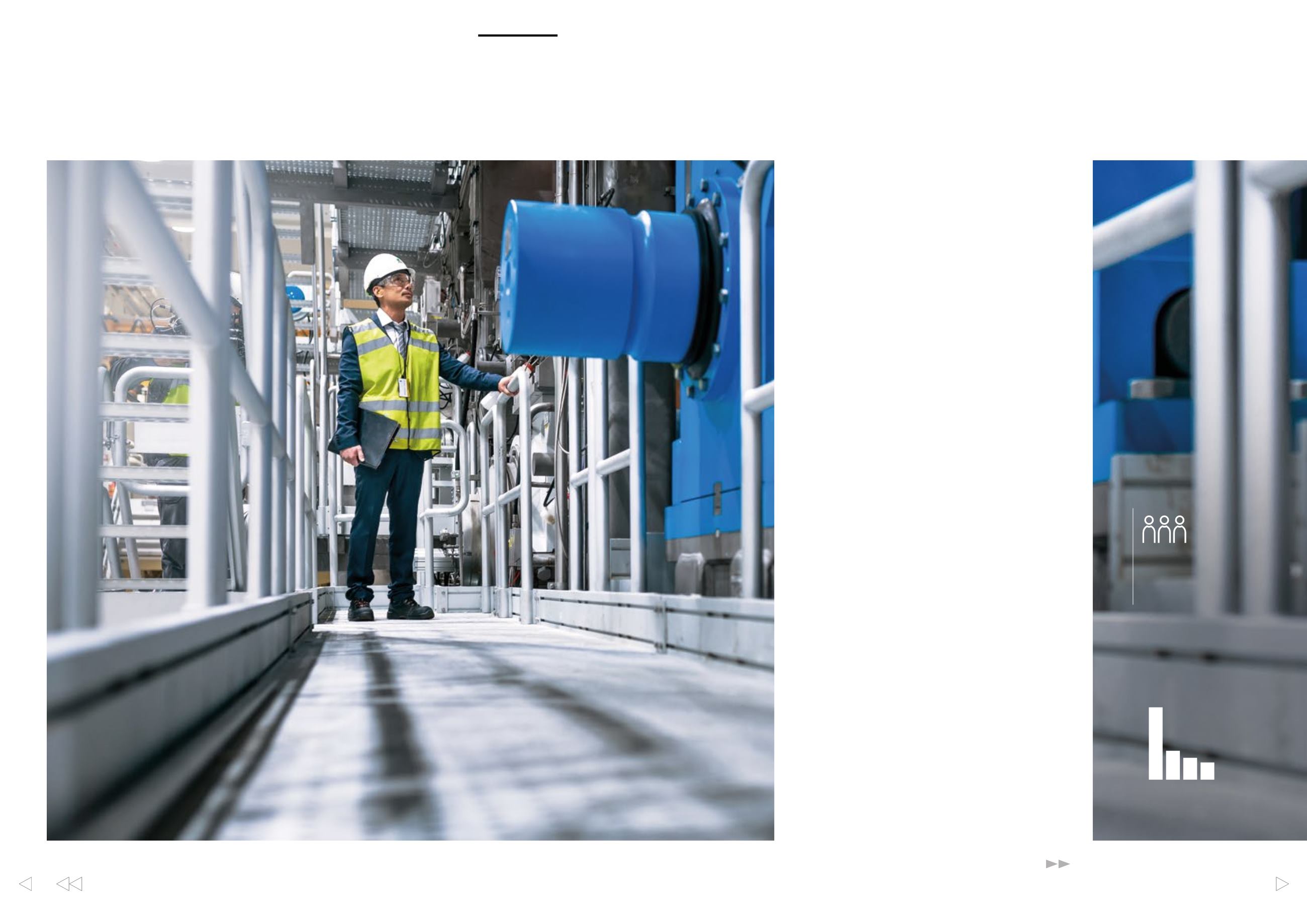
UPM Annual Report 2016
UPM Annual Report 2016
62
63
In brief
Strategy
Businesses
Governance
Accounts
Stakeholders
14 15 16
13
The number of environmental
deviations at UPM pulp
and paper mills
100
80
60
40
20
0
CONTENTS
Resource-
efficient
production
The company uses rawmaterials, water, energy and other resources in
a responsible manner and continuously improves its energy, production
and cost efficiency. Cost and material efficiency and good environmental
performance helps UPM to contribute towards achievement of several
UN’s Sustainable Development Goals (SDGs).
Almost all of UPM’s production plants, as well as its wood sourcing
operations, are covered by environmental, quality and occupational
health and safety systems, which are certified in accordance with the
ISO 9001, ISO 14001 and OHSAS 18001 standards. Additionally, several
production plants have an ISO 22000 food safety management system.
In order to improve energy efficiency, UPMhas introduced the
ISO 50001 certification system in Central Europe and a national energy
efficiency system (ETJ+) in Finland. In 2016, UPM’s pulp business area
developed a joint integrated management system for its four pulp mills.
A similar project has started for UPM’s paper mills in Finland.
UPMhas certified all its European pulp and paper mills, the UPMFray
Bentos pulp mill in Uruguay, and the UPMChangshu paper mill in China
in accordance with the EU Eco-Management and Audit Scheme (EMAS).
EMAS requires participants to have an Environmental Management
System and to publish a third-party verified Environmental Statement,
which increases the credibility and reliability of local environmental data.
Investments in environmental performance
UPM’s investments in environmental performance are part of the
Group’s investment programme. In 2016, the company’s environmental
investments totalled EUR 22 (28) million. The single largest investment
was UPM Schongau power plant retrofit to achieve lower air emissions.
UPM’s environmental protection costs totalled EUR 120 (129) million,
including depreciation. The main cost items were effluent treatment,
waste management, and air pollution control. Effluent treatment
amounted to EUR 48 (49) million, waste management to EUR 28 (34)
million, and air pollution control to EUR 5 (5) million.
Steady decline in number of environmental
non-conformances
There has been a significant decrease in the number of environmental
non-conformances since UPM’s internal Clean Run programme was
launched in 2012. Over 2,300 preventive environmental observations
were reported in 2016. The goal is to improve UPM’s environmental
performance, share best practices and promote environmental awareness.
In 2016, UPM introduced a global reporting tool, One Safety, for all
UPMers and contractors. The aim is to have a common, UPMway of
managing and reporting safety and environment-related operations.
One Safety tool covers environment, health and safety, product and
process safety as well as security. The tool was successfully implemented
at most UPM sites during the year.
No major environmental incidents occurred at UPMproduction
plants in 2016, and UPMwas not required to pay any significant fines
due to non-conformances. A total of 22 (28) temporary deviations from
permit limits or major deviations from the environmental limits set
by UPM occurred at the company’s pulp and paper mills over the course
of the year. The most significant single deviations were related to bio
logical sludge losses from effluent treatment plants or occasional odours
from pulp mills. UPM immediately reported deviations to local stake
holders and authorities, and undertook corrective measures to normalise
the situation and prevent similar situations from occurring in the future.
Certified management systems help UPM to control and improve
the performance of the company’s production facilities in matters
related to the environment, quality and health and safety.
2,300
preventive environmental
observations