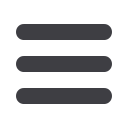

Welding technology
www.read-tpt.comJ
anuary
2015
81
Upgraded portable welding
KEMPPI has upgraded the Minarc
Evo equipment range. Minarc Evo 180
delivers more welding power than its
predecessor, the Minarc Evo 150, but
retains its qualities, serving ‘welders on
the move’.
The new Minarc Evo 180 has the
necessary power for MMA maintenance
welding, even where 4mm electrodes are
required. The portable 5.8kg machine
delivers 170 amps maximum output
current for MMA welding at 30 per cent
duty cycle, and 180 amps for DC TIG
welding at 35 per cent duty cycle. When
fitted with a 10-amp power supply plug
(market dependent) the Minarc Evo 180
still delivers 140 amps MMA welding
power at 28 per cent duty cycle.
Minarc Evo 180 includes power factor
correction (PFC) technology, giving
energy efficiency and maximum welding
power in any 1-phase, 230V, 16A or 10A
industrial power network. It can also be
used with generator power supply, even
with extra-long extension cables more
than 100m long. These qualities and its
light weight make it easy to use in many
welding jobs, in a wide variety of places.
A large LED meter display is included,
with a remote current control option,
and Lift TIG ignition as standard.
Precise arc ignition, large voltage
reserves and automatic arc dynamics
control make it suitable for welding with
all electrode types.
The Minarc Evo range offers a
choice of MMA, MIG/MAG, and DC
TIG welding equipment that is easy to
use and light to carry. The units include
Kemppi’s 2+ warranty cover.
Kemppi (UK) Ltd
– UK
Fax: +44 845 6444202
Email:
sales.uk@kemppi.comWebsite:
www.kemppi.comLaser welding opens new avenues
for process optimisation
THE Machines, Switzerland, has
several decades of experience in the
manufacture of extrusion lines for drip
irrigation pipe and tube systems, as well
as expertise in the field of transverse
and longitudinal laser welding of flat
sheet and tubular formed metals and
multi-layer metal polymer combinations.
Supply issues and unavailability of
helium, an essential forming gas in
the TIG welding process, is causing
concern and giving problems to a
number of industries engaged in metal
welding of sheet and tube, and multi-
layer pipe manufacturers. With the
expectation that the supply situation will
be further aggravated in years to come,
THE Machines has continued to drive
forward in the field of protection-gas-
free laser welding.
The traditional processing of metal
tape in the thickness range of 0.05 to
1.2mm in metal forming and stamping
plants is still discontinuous. This
means that a coil change mandates
not only a machine stop, but also a
time-consuming setup procedure each
time when re-threading the new tape.
This interruption of production could
be reduced by combining the end of
the tape with the incoming strip of the
new coil in such a way that the weld and
seam meet the rigorous requirements of
the subsequent process steps, eg line
tensions, repeated bending, forming
and heat treatment, securely and at
full production speed. The actual seam
can subsequently be left in the final
product, or may need to be cut out. This
optimisation potential has remained
untapped, since no suitable welding
method for joining the ends of thin metal
strips has been available to meet these
requirements.
THE Machines offers solutions for
cross-welding with the SLT range
of machines. The series covers a
bandwidth as standard from 80 to
750mm, with higher bandwidths
available on request. Laser welding is
particularly suitable for processing thin
sheets where other methods would
fail. The welding is conducted in fully
automated process steps. Depending
on the materials and thicknesses,
pre-programmed welding parameters
ensure high, repeatable quality. The
tensile strength and elongation at the
seam are generally ≥85 per cent of the
base material.
The LSL range of longitudinal laser
welding equipment is available in the
machine types 12, 40, 65 and 110 for
composite tube diameters up to 12mm,
40mm, 65mm and 110mm, and 12mm
for precision formed and welded tubular
metal structures containing optical fibres
such as those used in OPGW, OPPC,
FIST and other fibre optic applications.
An integrated optical seam tracking
system allows high process speeds,
and each LSL is suitable for the welding
of stainless steel or other alloys. The
quality of the entire seam integrity and
full weld depth and volume is checked
using latest multi-channel remote field
eddy current testing. The system uses
non-destructive testing and in-line
inspection of the weld seams with high
sensitivity to detect small and hidden
defects.
THE Machines Yvonand SA
–
Switzerland
Email:
info@the-machines.chWebsite:
www.the-machines.chThe SLT
range