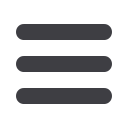

When the hydraulic and fuel lines on a single jetliner
can total 700 assemblies, the golden ideal of welding
and of tubemaking is identical: a faster weld at
no sacrifice in quality. Even orbital welding – fully
automated, versatile, offering perfect arc control – is
continually fine-tuned to deliver its benefits at ever-
higher speeds.
Tubemakers have mastered welding setups for
rotation, dwell, and penetration parameters, different
for each size of tubing. They know how to regulate
a power supply for welding current, primary and
background amperes, weld bead overlap, and for
delay of rotation at the start of the weld and current
downslope at the end. They share with welders
a zeal amounting to passion for a clean cutoff
operation with smooth surfaces and no contamination
or burring.
For as long as welding is the method by which tube
and pipe are joined, the advances that lie ahead for
the two already highly developed technologies will be
made in tandem. In the meantime, this partnership
of equals acknowledges a common obligation:
to provide perfect leak-tight joints having uniform
circumferential weld strength to the automotive,
defence, aerospace, biomedical and machine tool
industries of the world.
Welding technology,
equipment and
consumables