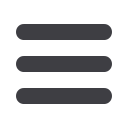

Welding technology
www.read-tpt.comJ
anuary
2015
77
Tube and pipe maker orders
giant induction welder
EFD Induction, a supplier of solid-state
welders, has reported a significant
delivery of a 1,800kW/300kHz welder to
a major tube and pipe manufacturer.
“It’s great news,” said Peter Runeborg,
head of sales at EFD Induction
operations in Norway.
“The order is from an extremely large
and well-known name in the global tube
manufacturing industry. We are proud
that they selected EFD Induction as
a partner to supply a large induction
welder.”
The news is even more significant
in light of the nature of the welder. Mr
Runeborg explains: “In terms of physical
size, the welder we built is the largest
ever constructed by EFD Induction.
We’ve previously built several welders
of similar power output. But as for
dimensions, this is the clear winner.
The welder is an 1,800kW welder for
large pipes, heavy-wall products.”
EFD Induction has, to date, installed
thousands of heating solutions for a
wide range of industrial applications,
bringing the benefits of induction
technology to many of the world’s
leading manufacturing and service
companies.
EFD Induction has manufacturing
plants, workshops and service centres
in the Americas, Europe and Asia.
Corporate headquarters are in Skien,
Norway.
EFD Induction
– Norway
Email:
knl@efdgroup.netWebsite:
www.efd-induction.comIncreased productivity with the
PERFECT
®
arc welding process
PERFECT
®
arc is a digital welding
process newly developed by PWS
GmbH. It can be used for spiral pipes as
well as for longitudinally seam welded
UO and JCO
®
pipes. It is suitable for
both arc and submerged arc welding.
The benefits: compared to conventional
welding procedures, PERFECT
®
arc is
50 per cent faster with tack-welding and
20 per cent faster with submerged arc
welding. This can mean a twofold or even
threefold increase in the productivity
of a spiral pipe plant, depending on
its design. It also offers considerable
energy savings. By controlling the power
supply precisely using the digital current
source, energy costs can be reduced
by more than 30 per cent compared to
conventional welding techniques.
Some of the applications for spirally
and longitudinally welded pipes include
gas and oil pipelines, shipbuilding and
wind turbines – particularly offshore
installations. To meet the ever growing
demands of these sectors, especially
in terms of high pressures or improved
resistance to corrosion, manufacturers
are increasingly turning to pipes made
from higher-strength steel grades. At the
same time this also means increasing
requirements with regard to the weld
seams and greater cost pressure on
pipe manufacturers. PERFECT
®
arc
now provides a solution that guarantees
high-quality weld seams, including
seams on higher-strength materials,
whilst delivering consistently high cost
efficiency.
In terms of the energy used,
PERFECT
®
arc offers an operating
efficiency level of around 90 per cent. For
plant owners this means energy costs
are reduced by more than 30 per cent.
At the heart of PERFECT
®
arc is a purely
digital current source, offering both ultra-
precise control of the power supply and a
superfast control intervention frequency
within microseconds. Processes are
controlled and managed with pinpoint
precision using Perfect
®
Control. This
control system integrates welding
control, wire feed rate control and the
evaluation computer within one unit,
thereby providing a closed-loop control
circuit. Problems with synchronisation,
such as those previously experienced
with multiwire submerged arc welding for
example, are thereby avoided.
In addition, PERFECT
®
arc allows the
power supply to be precisely controlled
during ignition, welding and stopping.
As a result, there is less spatter when
tack-welding, the seams are flush with
the pipe surface during submerged arc
welding, and cost savings can be made
as less material is used.
PERFECT
®
arc from PWS is
an innovative leap forward in the
production of spirally welded and
longitudinally seam welded UO and
JCO
®
pipes. The innovative, fully digital
process offers energy savings potential,
perfect weld seam quality and therefore
improved pipe quality too. The process
is said to be winning over customers
with its significant material savings,
considerably higher output and greater
flexibility when it comes to fast welding
process change-overs.
SMS Meer GmbH
– Germany
Fax: +49 2161 350 1862
Email:
info@sms-meer.comWebsite:
www.sms-meer.comTack welding
process during
pipe forming