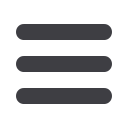

Technical article
March 2016
178
www.read-eurowire.comPrior to extrusion all materials, excluding
base resins, were dried in a vacuum oven
in the presence of desiccant (Dri-Rite:
anhydrous calcium sulphate) for 24
hours at 60°C. The dried materials were
then weighed and sealed in foil bags to
minimise moisture absorption and prevent
pre-cure or scorch during extrusion.
2.2 Wire Extrusion
Insulation coated wires were made using a
mini wire line extruder. The unit consisted
of a Brabender ¾" extruder with variable
speed drive, a 24:1 Maddox mixing head
screw, a Brabender cross-head wire die,
water cooling trough with air wipe, a laser
micrometer and a Con-Air variable speed
wire puller. All extrusions were done using
a 150°C flat temperature profile across the
three heating zones of the barrel as well as
the die.
A
layered
screen
pack
geometry
containing screens of 20/40/60/20 mesh
and a die plate were used to filter the
molten polymer just prior to reaching
the die opening. In addition, the screens
provided sufficient back pressure to
ensure better melt mixing of the various
formulations. A 67 mil (1.7mm) tip and
a 124 mil (3.15mm) die were used to
produce 14 AWG wires with a 30 mil wall
thickness. The same 67 mil tip was used
with a 174 mil (4.42mm) die to produce
coated wires with 60 mil of insulation.
Table 1
shows the head pressure, screw
and line speeds and melt temperatures for
each sample produced.
2.3 Moisture curing
All wires were cured in a 90°C water bath
for 18 hours to ensure full crosslinking.
Prior to flame testing the wires were
allowed to condition in a temperature and
humidity controlled room (25°C and 50%
RH) for 24 hours.
2.4 Burn Testing
Three cured and conditioned specimens
from each formulation shown in
Table 1
were subjected to FV-2/VW-1 burns in
accordance with UL Standard for Safety
for Wire and Cable Test Methods, UL25546.
Section 9.4 of the standard defines
the resistance of a wire to the vertical
propagation of flame and dropping of
flaming particles
[4]
.
24" wire specimens affixed with Kraft
paper strips at their tops were suspended
vertically in a draft-free chamber. A 37
±1 MJ/m
3
methane flame was impinged
upon the samples at an angle of 20° to
the vertical. The impingement point of the
flame was 254 ±2mm below the bottom
of the Kraft paper strip. A continuous
layer of surgical cotton was placed below
the specimens such that the surface of
the cotton was 235 ±6mm below the
impingement point of the flame.
Each specimen was subjugated to five
15-second applications of flame. The
interval between flame applications
was 15 seconds and the interval was
maintained for all applications where
the specimen self-extinguished prior
to the elapse of the 15 seconds. For
samples burning longer than 15 seconds
but shorter than 60 seconds, the next
application of flame was done when the
sample self extinguished. In order for a
sample to have passed the VW-1 burn test,
all of the following criteria must have been
met:
• Less than 25 per cent of the Kraft
paper indicator was burned
• The specimen did not burn longer
than 60 seconds after any of the five
applications of flame
• The cotton batting was not ignited by
either flaming or glowing particles or
flaming drops
In addition to these criteria, the burn
performances of the specimens in this
study were characterised by the following
parameters:
• Uncharred length – the distance below
the Kraft paper indicator that is not
burned and maintained a smooth,
unblemished surface after wiping with
a soft cloth
• Average burn time – the duration that
the specimen continued to burn after
the removal of the flame and averaged
over the five flame applications.
For burn durations greater than 60
seconds, the time was measured until
the Kraft paper began to burn
3 Results and
Discussion
3.1 Effect of insulation thickness
The effect of insulation thickness on the
performance of multiple compositions in
a VW-1 type test is shown in
Figure 1
for 14
AWG solid Cu conductors. The results show
that for the two higher flame- retardant
compositions, the burn duration decreases
as insulation thickness increases with
Sample Thickness
(mm)
Type
Press
(MPa)
Speed
(rpm)
Line
speed
(m/min)
Melt
temp (°C)
HB-1
0.76
Solid
10.5
50
2.7
159
VB-1
0.76
Solid
14.1
50
2.7
162
VB-2
0.76
Solid
15.1
50
2.7
159
HB-1
0.76
Strand
10.0
55
2.7
161
VB-1
0.76
Strand
13.9
55
2.7
161
VB-2
0.76
Strand
13.4
55
2.7
162
HB-1
1.52
Solid
10.1
80
2.1
160
VB-1
1.52
Solid
12.5
80
2.1
160
VB-2
1.52
Solid
11.8
80
2.1
160
HB-1
1.52
Strand
9.3
85
2.1
160
VB-1
1.52
Strand
12.9
85
2.1
160
VB-2
1.52
Strand
13.3
85
2.1
160
▲
▲
Table 1
:
Extrusion conditions of various moisture-cure constructions
▼
▼
Figure 1
:
Effect of insulation thickness on burn duration in VW-1 type test for different formulations
30 mil
60 mil
Burn duration (sec)