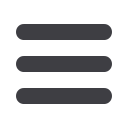

Technical article
March 2016
179
www.read-eurowire.comno burn time recorded for the 60 mil
insulation with VB-1 formulation. These
results are in line with the expectation
that for insulation or articles made
with flame-retardant materials, it is
increasingly difficult to start a sustainable
fire. The data also shows that for the less
flame-retardant material, ie, for HB-1
sample in this case, the opposite may be
true.
This observation can be easily explained
by the fact that below a minimum level of
flame-retardance when thicker materials
do catch and support a sustaining flame,
they will just burn longer because of
the larger mass of available flammable
material. For both cases with HB-1
formulation, the wire samples burn all the
way through the flag leaving no uncharred
length.
The effect of insulation thickness on the
burn behaviour can also be expressed by
the uncharred length of the samples as
shown in
Figure 2
. The results are shown
only for the VW-1 rated samples as the
horizontal burn rated sample burns
through the entire length of the wire
leaving no uncharred length. It is seen that
for both the formulations, the uncharred
length is higher for the thicker sample,
indicating a greater flame-retardance
with increase in thickness. The data also
suggests that VB-1 is better than VB-2 in
flame-retardance as evidenced by the
higher uncharred length and shorter burn
duration.
3.2 Effect of conductor type
(Solid vs stranded)
Even though a systematic study of the
effect of insulation thickness on burn
properties for low voltage wire is not
available in the literature, similar studies
have been conducted for other flame
retardant articles, an example of which
is fabrics for upholstery or children’s
clothing
[3]
. Comparison of such studies
with flame retardant wires needs to
be made with some caution since the
presence of a metallic conductor with
its high thermal conductivity provides a
thermal sink for the hot insulation and
adds to the complexity in understanding
the effects of various construction and
geometric parameters of the polymeric
layer.
In this study, another aspect of the
conductor, ie, solid vs stranded copper,
is investigated for its effect on the burn
behaviour of the wire.
Figure 3
shows the effect of the conductor
type on burn duration for all the
formulations in a VW-1 burn test for 30 mil
insulation thickness. For both the vertical
burn rated compositions, the flame
extinguishes much sooner for the solid
conductor than that for the stranded ones,
suggesting that using solid conductor
provides a better flame-retardance for the
wires. One possible reason for the superior
performance of the system with solid
conductor may be due to the intimate
contact it provides with the insulation,
thereby acting as a better dissipator of
heat from the polymer.
For the stranded conductors, on the other
hand, the voids between the polymeric
layer and solid copper act as thermal
insulation and thus trap more heat inside
the polymer. The difference is significant
since passing VW-1 burn test requires the
burn duration to be less than 60 seconds
for the samples. For both the vertical
burn rated formulations, when a stranded
conductor is used, the samples exceed
the maximum limit for burn duration, thus
failing the test.
In fact, for the VB-2 sample, the entire
length of the wire is consumed, leaving no
uncharred length (shown in
Figure 5
).
▲
▲
Figure 2
:
Effect of insulation thickness on uncharred length in VW-1 type test for different FR formulations (solid
conductors)
▼
▼
Figure 3
:
Effect of conductor type on burn duration for different formulations for 30 mil insulation thickness
▼
▼
Figure 4
:
Effect of conductor type on burn duration for different formulations for 60 mil insulation thickness
30 mil
60 mil
Uncharred length (mm)
Solid
Stranded
Burn duration (sec)
Solid
Stranded
Burn duration (sec)