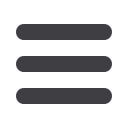

EuroWire – March 2008
211
english
Newmolybdate smoke
suppressant for PVC
By J Ken Walker, Wai-Kwong Ho, of Sherwin-Williams Chemicals
1. Introduction
Polyvinyl chloride, PVC, is an inherently
flame retardant polymer and is often used
in applications requiring low flame spread.
For some applications, the National Fire
Protection Association (NFPA) has also
established rigorous smoke standards. For
plenum rated PVC jacketing, communi-
cation cable must pass NFPA 262, the
Steiner Tunnel Test.
To qualify for use, flame spread must not
exceed 5 feet. In addition, peak smoke
must not exceed 0.5 units and the average
smoke throughout the test must be below
0.15 units.
Inorganic molybdates are the industry
standard for smoke suppression in PVC.
This is due to the inherent capability of
molybdates to promote char formation.
1-3
The most widely recognised molybdate
chemistry for smoke suppression in PVC
is ammonium octamolybdate, AOM.
Because of the high cost of molybdenum
and high percentage of molybdenum in
AOM (61% based on molybdenum oxide)
PVC manufacturers are looking for new
technology to increase the efficiency of
smoke suppression additives.
Ammonium octamolybdate is reported to
exist in two isomeric forms, designated as
alpha or beta. Typically, the α is the form
found commercially. This is manufactured
by the partial thermal decomposition of
ammonium dimolybdate, ADM according
to the reaction:
4 (NH
4
)
2
Mo
2
O
7
➞
(NH
4
)
4
Mo
8
O
26
+ 4 NH
3
+ 2 H
2
O
AOM has also been manufactured by
acidification of an ADM solution.
4-5
2 (NH
4
)
2
Mo
2
O
7
+ 4 MoO
3
➞
α -(NH
4
)
4
Mo
8
O
26
According to the patent literature, changes
in processing conditions can affect the
crystal structure. A new isomer, (designated
X-AOM) has been reported with improved
smoke suppression characteristics.
5
In addition to pure molybdate chemicals,
several engineered smoke suppressants
(KEMGARD) are manufactured and sold
by the Sherwin-Williams Chemicals Group.
These are typically based on zinc and
calcium molybdates, and are prepared
by precipitation in the presence of an
inert core.
6-7
The general concept of these engineered
materials is that precipitation onto the
surface of an inert mineral will increase the
surface area of the active chemistry and
reduce the total demand for molybdenum
in the PVC compound.
In light of the escalating price of molyb-
denum in the marketplace, engineered
smoke suppressants obviously become
more attractive.
In this work we report on the development
of a new engineered smoke suppressant
technology based on AOM chemistry.
We have found that the precipitation of
AOM in the presence of mineral extenders
can produce a new high surface area
AOM smoke suppressant. The high surface
area significantly increases the smoke
suppression performance over a standard
ammonium octamolybdate.
This advancement, which combines
Sherwin-Williams surface treatment tech-
nology and AOM chemistry represents a
significant advancement in AOM based
smoke suppression.
2. Materials
In this study several commercial AOM
smoke suppressants were examined.
These were also jet milled for further size
reduction and were included in our testing.
Table 1
shows the particle size and surface
area of the control materials tested.
High surface area AOM, Kemgard STA,
was prepared by reaction of ammonium
dimolybdate and molybdenum oxide in
the presence of an inert talc. The process is
described in an applied US patent.
8
Figure 1
:
SEM of Climax WA AOM
▲
Figure 2
:
SEM of Kemgard STA
▲