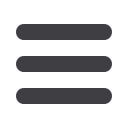

EuroWire – March 2008
212
english
Several inert fillers commonly used in PVC
compound were examined. Not all fillers
promoted the formation of high surface
area AOM. In this work, we describe only
the results obtained with a talc filler.
X-ray diffraction was carried out on KG-STA
and commercial AOM. The AOM in KG-
STA and that in the commercial material
was indistinguishable. SEM analysis did
indicate a difference in particle shape and
morphology for KG-STA and commercial
AOM.
Figure 1
shows an SEM image of
a commercial AOM WA from Climax.
Figure 2
shows the structure of Kemgard
STA. In the commercial material, the AOM
is found in the form of irregularly shaped
agglomerates. However, in the KG-STA
samples, the AOM is found in the form of
distinct rods.
Based on the SEM micrographs, it appears
that the precipitation of ammonium
octamolybdate in the presence of talc
promotes the formation of rods rather
than agglomerates. How the presence of
talc influences the morphology of AOM,
thermodynamically or kinetically, is not
yet understood.
As measured by the BET method, the rod-
like structure of AOM in Kemgard STA has
higher surface area than the commercial
materials. The surface area values of
the various AOM products are shown in
Table 2
.
The surface area of a blended material
can be considered an additive property.
For example, a blend of talc and Climax
AOM WA is calculated as a weighted
average of the individual components,
as shown in
equation 1
.
Talc+AOMWA=0.3*(13.8)m²/gm+0.7*(1.6)m²/gm
= 5.26 m²/gm
Equation
(1)
The calculated value of 5.26 m²/g compares
favorably with the experimentally deter-
mined value of 5.1 m²/g.
For KG-STA, the experimentally determined
BET surface area was 7.0 m²/gm. Using the
same rule of mixing, the contribution from
the surface modified AOM is calculated to
be equivalent to 4.09 m²/gm, as shown in
equation 2
.
STA AOM =[7.0 m²/gm – (0.3 * 13.8 m²/gm)] / 0.7
= 4.09 m²/gm
Equation
(2)
Therefore, the ammonium octamolybdate
of KG STA is determined to have a surface
area 1.5 to 2.5 times higher than the two
commercial grades of AOM.
One technique of increasing surface
area is by reducing the particle size via
mechanical milling. Although this is a
common practice, there is a diminishing
rate of return as controlled by energy
cost, stability of product and material
integrity during processing. Both grades
of commercial Climax AOM were jet milled
and compared to the KG STA in
Table 3
.
Jet milling failed to decrease the particle
size or increase the surface area of Climax
AOM A2. However, with the larger par-
ticle Climax AOM WA, jet milling did
produce considerable improvements in
both surface area and particle size.
Nevertheless, the surface area of the twice
jet milled AOM-WA was still 10% lower
than the calculated value for KG-STA. The
higher AOM surface area of KG-STA is
expected to result in greater effectiveness
of smoke suppression. Char formation in
PVC is catalysed by molybdate; therefore
higher surface area should produce higher
char yield.
3. Test Methods
3.1 ASTM E662 NBS Smoke Chamber
The release of smoke generated by the
combustion of plastic materials can be
determined using the National Bureau of
Standards (NBS) smoke chamber method,
standardised in the United States as
ASTM E662.
This test was originally developed
to determine the smoke generating
characteristics of plastic materials used in
aircraft construction.
Average Particle Size
(D50)
BET Surface Area
Climax A2017I
0.68 micron
2.9m
2
/gm
ClimaxWA011GA
3.26
1.6
HC Starck 02F001
0.68
2.7
Table 1
:
Particle size and surface area of commercial AOMs
▲
Table 2
:
BET surface area measurements
▲
Talc
Kemgard
STA
Climax
AOM
WA
Climax
AOM
A2
Talc +
Climax
AOM
WA
13.0
m
2
/gm
7.0
m
2
/gm
1.6
m
2
/gm
2.9
m
2
/gm
5.1
m
2
/gm
Kemgard
STA
Climax
AOM
WA
Climax
WA
(2 passes)
Climax
AOM
A2
Climax
A2
(1 pass)
BET
(m
2
/gm)
7.0
1.6
3.7
2.9
2.9
PSD D50
(micron)
2.74
3.26
0.71
0.68
0.57
Oxyvinyl 240F
100
100
Halstab H-695
7
7
Sb
2
O
3
3
3
Micral 9400
30
60
Santicizer 2148
20
20
Uniplex FRP-45
20
20
Table 3
:
Surface area and particle size measurements
▼
Table 4
:
Flexible PVC formulations
▼