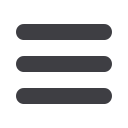

EuroWire – January 2011
55
technical article
2 Zinc phosphates
Currently there are three types of zinc
phosphate commonly in use. These are
defined by their means of acceleration.
They are:
Nitrite/nitrate
•
Chlorate/nitrate
•
Nitrate/air (Fe side process)
•
Nitrite/nitrate is the most widely used
outside Central Europe. The system
operates at high temperatures producing
sludge that settles at the bottom of the
process tank. The most common form
of accelerator is sodium nitrite. These
processes commonly contain nickel, which
acts as a refining agent.
Chlorate/nitrate
processes
are
used
for specific situations where either the
operation is more suited to this method of
acceleration, such as intermittent working,
or the phosphate produced meets a
particular demand. Sludge is also produced
in the process tank by this system.
Nitrate/air (Fe side processes) operate at
lower temperatures and produce their
sludge in an external tank into which a
controlled supply of air is introduced.
The sludge produced is hard and dense,
and settles readily at the bottom of the
tank. These processes are nickel and nitrite
free.
3 Activation
To obtain the maximum benefits from
a zinc phosphate coating the use of an
activator prior to the zinc phosphate
is highly recommended. The activator
provides sites for the nucleation of the
zinc phosphate crystals, which pro-
duces a refined, controlled, crystalline
coating.
This will lower the coefficient of friction
and improve the adhesion of the coating
to the metal surface.
The fine crystal structure also increases
the available surface area for the
subsequent lubrication process.
4 A new type of
lubricant as an
alternative to
soaps and MoS
2
The new lubricants are high performance
polymer systems. Applied by immersion
in an aqueous solution they produce thin
organic coatings.
For
maximum
performance
results
this lubricant is best used on top of a
conversion coating. Application on bare
material is possible but must be examined
on a case-by-case basis and thus cannot
be generalised.
The chart above shows the coating
thickness as compared to the conventional
lubricants used so far.
4.1 Objectives of the new development
The general target was to develop a
coating that allows net shape forming
without any negative impact on the tool
life. This means that the forming accuracy
should be appreciably better than that
obtained when using soap, and should be
at least equivalent to that obtained with
MoS
2
.
Moreover, the goal was to achieve a
coating that is substantially cleaner and
easier to remove. The lubricant concentrate
should be classified in the lowest water
hazard class and no additives were to
be used that may present a potential
corrosion risk.
Comparison of the coating thickness
of various lubricants
Comparison of the coating thickness of various lubricants
Lubricant layer g/m
2
Polymer
MoS
2
Soap
Figure 2
▲
▲
:
Comparison of the coating thickness of various lubricants
Cross-section of a treatment plant
Return flow
Feed calcium
phosphate
Grid anodes
Phosphating solution
Cathode
Wire and solid part
Figure 3
▼
▼
:
Cross-section of a treatment plant