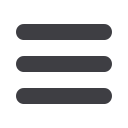

EuroWire – Januar 2011
60
technischer artikel
Die zu bearbeitenden Teile werden
nochmals gespült, neutralisiert und zuletzt
wird ein Schmiermittel aufgetragen.
Die Schmiermittel sind wasserlösliche
Seifen, die mit der Umwandlungsschicht
reagieren, oder anderenfalls die Disper-
sionen von Molybdän-Disulfid (MoS
2
). Für
den kompletten Verfahrensablauf werden
zwischen 60 und 90 Minuten angesetzt.
Es ist beachtenswert, dass die Qualität
von Phosphat, und die darauf folgenden
Leistungsergebnisse, eine Reflexion der
Pflege darstellen, die in den früheren
Verfahrensphasen aufgewendet wurde.
2 Zinkphosphate
Derzeit
gibt
es
drei
Typen
von
Zinkphosphaten, die allgemein verwendet
werden.
Sie
werden
durch
deren
Beschleunigungsmittel festgelegt, bzw.:
Nitrit/Nitrat
•
Chlorat/Nitrat
•
Nitrat/Luft (Fe-Sekundärverfahren)
•
Nitrit/Nitrat ist das am meiste außerhalb
Mitteleuropa eingesetzte. Das System
läuft mit hohen Temperaturen und
erzeugt Schlamm, der sich am Boden des
Verfahrenstanks ablagert. Die gängigste
Beschleunigungsform ist Natriumnitrit.
Diese Verfahren enthalten üblicherweise
Nickel, der als Raffinationsmittel wirkt.
Chlorat-/Nitrat-Verfahren
werden
in
besonderen Fällen benutzt und zwar
dort wo sich das Verfahren dieser
Beschleunigungsmethode besser anpasst,
wie z. B. bei unregelmäßigen Vorgängen,
oder wo das hergestellte Phosphat eine
besondere Anforderung erfüllt. Durch
dieses System wird auch Schlamm im
Verfahrenstank erzeugt.
Nitrat/Luft (Fe-Sekundärverfahren) agiert
bei niedrigeren Temperaturen und erzeugt
deren Schlamm in einem Außentank, in
dem eine kontrollierte Luftversorgung
eingeführt wird. Der erzeugte Schlamm
ist hart und dicht, und lagert leicht am
Tankboden ab. Diese Verfahren sind nickel-
und nitritfrei.
3 Aktivierung
Um die meisten Vorteile von der Zink-
Phosphat-Beschichtung zu erzielen ist
der Einsatz eines Aktivators vor dem
Zink-Phosphat
sehr
zu
empfehlen.
Der Aktivator bietet die Stellen zur
Kernbildung der Zink-Phosphatkristalle an,
die wiederum eine verfeinerte, geprüfte,
kristallartige Beschichtung erzeugt. Somit
wird der Reibungskoeffizient gesenkt
und die Haftung zwischen Beschichtung
und Metalloberfläche verbessert. Die
feine Kristallstruktur erweitert auch den
verfügbaren Oberflächenbereich für das
darauf folgende Schmierverfahren.
4 Ein neues
Schmiermitteltyp als
Alternative zu Seifen
und MoS
2
Die
neuen
Schmiermittel
sind
Hochleistungs-Polymersysteme.
Durch das Tauchen in eine wässrige
Lösung aufgetragen, erzeugen sie dünne
organische Beschichtungen. Für die
höchsten Leistungsergebnisse werden
diese Schmiermittel am besten oberhalb
der Umwandlungsbeschichtung benutzt.
Die Auftragung auf Blankmaterial ist
zwar möglich, muß aber Fall für Fall
untersucht werden und kann daher nicht
verallgemeinert werden. Das nachfolgende
Diagramm zeigt die Beschichtungsdicke
im Vergleich zu traditionellen, bis heute
benutzten Schmiermitteln.
4.1 Ziele der neuen Entwicklung
Das Hauptziel lag darin eine Beschichtung
zu entwickeln, die eine Konturformgebung
ermöglichte ohne eine negative Wirkung
auf die Lebensdauer der Werkzeuge zu
verursachen. Das bedeutet, dass die
Genauigkeit der Umformung durchaus
besser sein sollte als jene die beim Einsatz
von Seife erzielt wird. Sie sollte zumindest
jenen entsprechen, die mit MoS
2
erzielt
wurden.
Die Zielsetzung lag außerdem darin, eine
Beschichtung zu erzielen, die wesentlich
sauberer ist bzw. leichter zu beseitigen ist.
Das Schmiermittelkonzentrat sollte in den
niedrigsten
Wassergefährdungsklassen
eingestuft werden. Dabei sollten keine
Additive benutzt werden, die eine
mögliche
Korrosionsgefahr
darstellen
könnten.
4.2 Chemische Grundsätze der neuen
Beschichtung
Die neuentwickelte Polymerbeschichtung
ist eine Mischung von hochmolekularen
Compounds, die frei von Schwermetallen
sind
sowie
von
Bor-Mischungen,
Mineralöl, chlor- oder schwefelenthaltende
Schmiermitteladditive
(wie
z.
B.
Molybdän-Disulfid,
Hartmetall-Disulfid)
oder auf Fluor basierende Compounds, z.
B. Teflon®.
4.3 Vorteile für den Kunden
4.3.1 Vorteile der Polymerbeschichtung
für Drahthersteller oder Vor-Benutzer von
Stabquerschnitten
Vergleich der Beschichtungsdicke
diverser Schmiermittel
Schmiermittelschicht g/m
2
Polymer
MoS
2
Seife
Bild 2
▲
▲
:
Vergleich der Beschichtungsdicke diverser
Schmiermittel
Querschnitt einer Behandlungsanlage
Rückfluss
Zuführung von
Kalziumphosphat
Gitteranoden
Phosphatierungslösung
Kathode
Draht und festes Teil
Bild 3
▼
▼
:
Querschnitt einer Behandlungsanlage