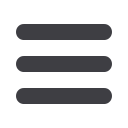

30
M
ay
/J
une
2007
Technology
Update
Lazzari is an Italian producer of circular
sawing machines for the cutting of steel and
non-ferrous metal. The company recently
received an order from an Italian customer
to modernise the equipment on the finishing
line of its pipe mill.
The order specified cutting with circular
sawing machines that work inline with
the mill, provide enough capacity to cover
the output of the mill and achieve a good
finished cut. It also required charging and
discharging of the tube layers.
To meet these requirements, the technical
staff at Lazzari designed a sawing machine
with a range of features. These include a
machine bed and structure to resist high
loads; a clamping system to clamp in front
of and behind the saw blade with controlled
position and pressure (to eliminate tube
vibration); and heavy duty guides for the
sawing head for maximum stiffness. A
heavy duty gear box is also included with a
special system to automatically compensate
for the backlash.
Several anti-dumping devices give guidance
to the saw blade, so that vibrations are
eliminated, giving a smooth cutting surface
and longer tool life. A micro-spraying system
ensures optimal blade lubrication, and chips
are cleaned from the teeth of the saw blade
by brushing devices. Extra cooling of the
saw blades allows hot tubes up to 200° to
be processed.
The charging device features swivelling
arms for loading tubes onto the inlet roller
way, while length measuring stoppers
ensure tight length tolerances.
Two model VRS 1400 sawing machines
were installed in the finishing line, along
with an additional two external clamping
devices at the in-feed and out-feed side of
the sawing machines, to guarantee perfect
clamping of the tube layer.
The complete process is computer
controlled: the system recognises the
incoming material quality and the sawing
machine automatically chooses the correct
cutting parameters. The tube layer is cut
to the input finish length and fed out of the
machine, and the head and tail crop ends
are automatically discharged.
Lazzari SpA
– Italy
Fax
: +39 035 4375175
:
info@lazzarigroup.comWebsite
:
www.lazzarigroup.comTurnkey high performance
testing and cutting lines
Reika, Germany, has received a follow-
up order for a turnkey NDT system from
Europe’s largest producer of seamless steel
tubes. The whole line will be directly linked
to a straightening line with large buffer area
and inlet conveyor system. Start-up of the
complete line is due to be carried out within
4 weeks.
Before testing on the NDT system, loose
scale and chips are removed from the tube
after straightening and cutting operations.
The tubes are individually transported
at high-speed into the multi-testing
NDT-section, running continuously at a
180m/min throughput rate.
Inline continuous electrolytic pickling
for stainless steel tubing
Condoroil, Italy, has launched a new induced current pickling tunnel for stainless steel
tubing. The new system allows the completion of various phases of the pickling process,
including degreasing, pickling/passivation and rinsing, up to marking and packaging
directly on the production line, without any further handling.
An induced current electrolytic process
inside the tunnel uses a new formula
pickling solution. This solution is made
with Descalinox P23, which contains no
hydrofluoric acid or nitric acid.
Advantages are reflected both in
economy, with savings in raw materials
and energy costs, and in the working
schedule, where all intermediate
handling phases are eliminated. The
complete automation of inline operations
and the new formula chemicals are
expected to improve accident prevention
and environmental protection. This is
because use of a pickling solution made
with Descalinox P23 improves working
conditions and reduces the risks related
to the handling of solutions during
manufacturing and stocking.
Condoroil Impianti Srl
– Italy
Fax
: +39 0332 967 598
:
info@condoroil.itWebsite
:
www.condoroil.com›
Condoroil has developed a new induced current
pickling tunnel for stainless steel
Heavy duty circular sawing machine
for cutting tubes in layer
›
A circular sawing machine from Italy’s Lazzari
fi
Reika’s turnkey NDT system for seamless steel
tubes