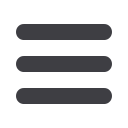

Technology
Update
36
M
ay
/J
une
2007
Huntingdon
Fusion
Techniques Ltd, UK,
provides
the
cost-
efficient
technology
to keep welds clean
while welding. This
technology can be used
in cases where piping or
pipelines are fabricated
from stainless steels,
reactive alloys, nickel
alloys, nimonics and
titanium.
By adding a lightweight
component called a
‘Trailing Shield’ to a TIG/
GTAW welding torch
the weld stays under a protective Argon
Gas shroud, while the hot, welded joint is
cooling. This prevents the heated metal
from oxidizing on contact with air. Trailing
Shields are available for any diameter of
pipe.
Replaceable silicon rubber seals are
used on the sides of the Trailing Shields
to prevent the protective argon gas from
escaping.
Each Trailing Shield is delivered with
variable diameter connector so that it can fit
any size of TIG/GTAW/PAW welding torch
whether for manual or mechanised welding.
Huntingdon Fusion Techniques Ltd
– UK
Fax
: +44 1554 836837
Emai
l:
hft@huntingdonfusion.comWebsite
:
www.huntingdonfusion.comIndian piping supplies
Shripal Metal Ltd, India, supplies piping
material and other ferrous and non-ferrous
construction materials to industries including
petrochemicals, fertilisers, refineries, oil and
engineering. The company has undertaken
a substantial quality assurance initiative,
and is a pioneer in the implementation
of the bar coding system on material to
provide accurate tracking.
The company has actively participated in
various national and international exhibitions,
including wire & Tube Düsseldorf 2006 in
Germany, and Chemcon-Summit 07 – India.
Shripal Metal Ltd
– India
Fax
: +91 22 2242 8765
:
shripalm@bom2.vsnl.net.inWebsite
:
www.shripalmetals.comAutomatic feed table for collaring machine
T-Drill, the manufacturer and supplier of tube processing and chipless tube cutting
machines, has made a number of improvements and additions to its model S-54
collaring machine.
For branching of manifolds, T-Drill has introduced a new automatic feed table (AFT)
that can store up to 99 different branching specifications. It has a positioning efficiency
comparable to typical CNC controlled configurations. The new AFT is also equipped with
a universal clamping system that reduces tooling costs and set-up times.
Typical uses for the new S-54 with AFT include air-conditioning, floor heating and solar
panel manifold applications. The T-Drill collaring method improves the quality of tube
joints, and makes brazing operations easy to carry out, since the collar fixes the branch
tube in the correct position, allowing brazing without other fixtures.
T-Drill Oy
– Finland
Fax
: +358 6 4753 300 •
:
sales@t-drill.fi•
Website
:
www.t-drill.fiT-Drill Industries Inc
– USA
Fax
: +1 770 925 3912 •
:
t-drill@t-drill.com•
Website
:
www.t-drill.comPipe welds made bright and shiny
Highly productive and
fully automatic short tube
manufacturing
The production of short tubes with high
productivity, flexibility and quality is the
focus of weil engineering GmbH, Germany.
The company has perfected the design
and construction of rollforming and welding
machines to produce finished tubes from
blanks.
A wide variety of laser, TIG or plasma weld
sources can be applied for welding. The
WE product range covers tube dimensions
from 25mm to 1,000mm in diameter, up to
2,000mm in length and 0.2-3mm in wall
thickness. The WE roll forming machines
are NC controlled to allow a high shape
flexibility. The welding machines incorporate
a fully automatic, flexible and accurate
clamping system for high product quality
and constant repeatability. Automation
components are available for all machines
allowing a lean production.
Weil engineering GmbH have recently
launched their latest development, branded
the Ecomaster, a manufacturing cell
combining rollforming and welding into
one compact unit. The scope of operation
for the Ecomaster covers diameters from
80-200mm, tube lengths from 80-500mm
and wall thickness from 0.8 to 2mm.
A special feature of the Ecomaster is the
multiroller rollforming unit for tube shaping,
which allows production of different
diameters without any part change.
For any change of diameter, all that is
required is the connection of a suitable
tool into the welding unit and adjustment of
the blank feeding into the rollforming unit.
Changeover time for diameter change is
only about 18 minutes, and only 5 minutes
for the change of tube length.
Upon request, a range of welding sources
can be offered, including laser. With the
basic model, blanks are fed manually
onto the infeed table, which allows an
efficient entry into the automated short
tube manufacture. With the option of an
additional destacker the automation of blank
feeding is possible; when feeding from one
destacking position, the second destacking
position can be refilled.
weil engineering GmbH
– Germany
Fax
: +49 7631 1809 49
:
info@weil-engineering.deWebsite
:
www.weileng.com›
Huntingdon’s Trailing Shields are used to keep welds clean