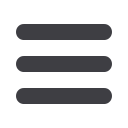

Technology
Update
32
M
ay
/J
une
2007
George A Mitchell Company, USA, has
been contracted to design and build two
complete lines of forming equipment.
This equipment will be used to produce
variable wall/variable OD cylinder blank
tubes for a major parts supplier to the auto-
motive industry. A cylinder blank tube
is an integral part of the power steering
assembly.
Each of the two lines will be capable of
producing more than one million parts per
year. The unique manufacturing process is
carried out by several forming procedures.
Mitchell is considered an industry expert in
the field of tube push pointing, tube drawing
and tubular extrusion.
The forming equipment is specifically
designed for the purpose and shall be tooled
for eleven different parts. One forming
system includes four forming stations with
an automatic tube lift and carry handling
mechanism. A 1,000 gallon pumping unit
with a total of 170 HP and eleven Vickers
pumps powers the equipment hydraulically.
The extruding stations each utilise specially
designed extrusion mandrels and carbide
dies, along with linear displacement
transducers for programming linear tooling
positions. An Allen Bradley PLC along with
a human-machine interface operator panel
controls the forming cell.
The new forming process makes the current
procedure obsolete, which utilises multiple
vertical presses. The cost savings in the
manufacture of the product is achieved
through automatic material handling and
overall reduction of cold forming operations.
The starting tube is welded, annealed and
prelubricated, with no intermediate lube
required in the Mitchell operation. The total
percentage area reduction achieved for
certain parts is over 68 per cent.
For the past few years, the company has
been a leading provider of production
equipment for variable wall tubes used in
making SUV and truck axles, as well as
instrument panel beam tubes and ball bats.
New developments are currently underway,
with cold forming processes designed for
manufacturing utility poles up to 70ft in
length and multiple wall furniture leg tubes.
Mitchell is also an industry leader in push
pointing technology with more than 44
years of machine design and manufacturing
experience, with successful installations in
29 countries throughout the world.
George A Mitchell Company
– USA
Fax
: +1 330 758 7263
:
sales@mitchellmachinery.comWebsite
:
www.mitchellmachinery.comSmall diameter
thin wall tubes
High Tech Tubes Ltd, UK, supplies high
quality, small diameter and thin wall tubes to
the aerospace, electronics, instrumentation
and medical industries.
The company is an independent
manufacturer, specialising in producing
non-standard tubes with tight tolerances
in aluminium, OFHC and DHP copper,
brass, cupro-nickel, nickel/nickel alloys and
stainless steel. Outside diameters range
from 0.25mm/0.01" to 16mm/0.625".
The company also produces profile tubes,
including square, rectangular, hexagonal,
elliptical, oval, triangular and half-round
sections. Quality assurance is covered
by ISO.9001:2000 and the International
Aerospace standard AS.9100:2001.
High Tech Tubes Ltd
– UK
Fax
: +44 1932 355 441
:
sales@hightechtubes.co.ukWebsite
:
www.hightechtubes.comOrbital machines for cutting,
bevelling and welding
Axxair, France, develops and manufactures
orbital machines that allow users to cut,
bevel and weld tubes with the same
machine. The Global Concept covers all
orbital operations applied to tubes, enabling
users to make a step-by-step investment.
The machines can be equipped according
to user requirements, with all relevant
training and servicing.
For 10 years, the company has offered
technology including a large range of
cutting machines (with integrated greaser),
large diameter capacity per machine, and
a single concentric patented clamping
system with stainless steel clamps.
They also supply a new patented orbital
bevelling system with carbide tips, and a
single range of welding machines for pre-
fabrication.
The company’s machines are sold
worldwide through a network of qualified
Axxair partners, who supply to industries
including food, pharmaceutical, and
cosmetics.
Axxair
– France
Fax
: +33 4 75 57 50 80
:
marketing@axxair.comWebsite
:
www.axxair.comAutomotive forming lines
for power steering cylinder blank tubes
›
A Mitchell serial PP-677 multistation tubular
extrusion system
›
A cross section of formed cylinder blank tubes