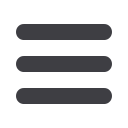

Technology
Update
34
M
ay
/J
une
2007
German steel and metal distributor,
Klöckner & Co, is responsible for the first
stage of metal preparation for automotive
manufacturers and their component
suppliers. The plant produces components
of any shape and dimension, including flat,
square and round material, tubes, solid bars
and sections of different materials. Between
40-50t of processed material leaves the
preparation centre daily.
A completely modular sawing centre from
machine manufacturer RSA, Germany,
was designed to ensure smooth running
of Klöckner’s manufacturing flow. For this
purpose, the Rasacut sawing centre unites
several working steps: sawing, deburring,
checking, and commissioning.
To complement the Rasacut, the company
also supplied the Rasacheck measuring
system to check the length of tubular
workpieces, and supervise the process.
The 100 per cent measuring of the RSA
system avoids the delivery of any defective
parts, instead of relying on calculations of
probability.
The length measuring system, which
is integrated into the sawing centre,
automatically ejects every faulty piece on
the spot. If a freely definable maximum
quantity of defective workpieces is produced
in sequence, the whole sawing centre shuts
down in order to avoid rejections.
The measuring module requires no
setting up or adjustment work, and can
be linked to any other brand of machine
or integrated into any production line.
The measuring data can be transmitted
to any QA software, or documented and
analysed by RSA software. Documentation
of measuring data and statistical
computations are available on CD,
hardcopy, or can be sent to a third party
via remote data transmission.
United processes:
sawing, deburring and checking
fi
The Rasacut modular sawing centre from RSA
›
The Rasacheck module measures up to 5,000
parts per hour, and automatically ejects faulty
parts
fi
The Rasacut sawing centre consists of inde-
pendent modules which can be freely combined
and extended