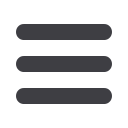

Fig. 1 Highly insulated DC/DC converters optimise power supply
to IGBT and SiC-FET drivers in power electronics
was eliminated by the development
of IGBTs or insulated date bipolar
transistors. As the name suggests,
this is a combination of MOSFET at
the input and bipolar transistor at the
output, providing the best of both
worlds. Like MOSFETs, IGBTs operate
almost without control current,
and have low voltage drops on the
collector and emitter paths in their ON
state as is typical of bipolar transistors
allowing them to switch high voltages
and currents while keeping losses
very low.
SiC-FETs are ideal for
higher power and higher
frequencies
IGBTs use monocrystalline silicon as
a semiconductor material compared
to silicon carbide in SiC-FETs. Silicon
carbide has a higher melting point
and allows much thinner insulation
layers at the gate, which improves
thermal conductivity and allows
higher power density. The switching
losses in SiC-FETs are lower than
IGBTs by a factor of at least four (Fig.
2) – an advantage that especially pays
off in higher performance ranges and
higher switching frequencies.
SiC-FETs will still only dominate in the
high-performance range due to cost,
and will not be able to drive IGBTs out
of the mass market.
Insulated DC/DC
converters ensure
optimised power supply
As mentioned above, control quality
is the main determinant in switching
losses, so gate drivers and their power
supply deserve special attention. Input
signal and power supply to driver
ICs need very effective insulation as
they are directly coupled to the high
potential in the IGBTs or SiC-FETs;
insulated DC/DC converters provide
an especially convenient solution in
the latter.
Commercially available driver modules
are asymmetrically controlled by
positive and negative voltage.
However, IGBT and SiC-FET drivers
differ in the voltage levels required.
Data sheets quote threshold voltages
of +3V for For IGBTs. In practice,
however, quick, clean switching
requires +15V, even requiring a
negative bias voltage on the gate to
switch off securely and prevent an
undesired restoration of power due to
the high dV/dt load. In practice, -9V
has proven to be a safe bias voltage.
Converters with voltages from +15V
and -9V are therefore required for
supplying IGBT drivers (Fig. 3, left).
SiC-FETs raise a somewhat different
situation as their switching thresholds
are between +1V and +2V. A gate-
source voltage of +20V makes
sense to keep conductive losses
(RDSON) to a minimum – settling for
a conventional +15V value for IGBTs
would increase RDSON losses by up
to 30%. A negative voltage of -5V has
established itself as ideal for them to
switch off reliably (Fig. 3, right). A
more negative voltage would result in
a change in gate-source parameters,
leading to impaired stability.
High dV/dt places a
strain on the insulation
barrier
A DC/DC converter’s insulation can be
visualised as a dam dimensioned for a
certain maximum level – a dam that is
high enough will withstand the waves
in a storm surge, but flooding even at
places will cause a breach.
A DC/DC converter behaves the same
way. High switching frequencies –
New-Tech Magazine Europe l 57