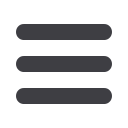

23
Chemical Technology • March 2015
They use chemical vapour deposition. The phones are
placed in a vacuum chamber under low pressure, and a
plasma pulse is used to ‘activate’ the surfaces to be coated
(ie, allow them to become charged). The fluoropolymer gas is
introduced where it forms covalent bonds with the surface.
A pulsed radio frequency plasma polymerises the coating to
form the layer.
Obviously, such a surface will not stand abrasion, but the
parts of a phone you want to waterproof are on the inside.
These surfaces are not ‘permanent’ and P2i imagines that
their coating system will be incorporated in devices that they
hope will become as ubiquitous as a microwave oven. P2i
have also used their technique to coat air filter media for the
oil industry where Teflon (PTFE, the original fluoropolymer
coating) is normally used.
Simply put, though, this approach is too expensive. On high-
margin goods like phones, fine, but howabout if all youwant to
do is get the last drops of premier tomato sauce out the bottle?
Professor Kripa Varanasi and his team at MIT have de-
veloped a liquid-impregnated surface which can be coated
onto the inside of pipes and bottles. Their coating creates a
permanent liquid layer against a porous solid coating over the
original surface. They have a YouTube video of tomato sauce
pouring out of a bottle that has a voodoo-like look.
The problem with these sorts of additive coatings is that
they have a very short life-span and don’t handle abrasion or
temperature variation without degrading. The applications
where superhydrophobic surfaces would be of greatest value
are industrial. Think aircraft wings that don’t ice-up (the cause
of numerous disasters), turbine bladeswith improved longevity
and resistance to abrasion, ship hulls that don’t foul and so
improve fuel economy and speed, hospital medical devices
which are intrinsically sterile and prevent bacterial growth,
solar panels which are uniformly black at any angle and low
maintenance.
Cornell University and Rensselaer Polytechnic Institute are
using the electrochemical process of anodisation to create
nanoscale pores. These, they believe, change the electrical
charge and surface energy of metal surfaces, which then
repels bacterial cells and prevents thin-film formation.
In "Alumina surfaces with nanoscale topography reduce at-
tachment andbiofilmformationby
Escherichia coli
and
Listeria
spp
", Guoping Feng,
et al
, present their research. Importantly,
the approach is low-cost and results in a ‘generally recognised
as safe’ material. The pore sizes they achieve are in the range
of 15 to 25 nm.
“It’s probably one of the lowest-cost possibilities to manu-
facture a nanostructure on a metallic surface,” said Carmen
Moraru, associate professor of food science and one of the
paper’s senior authors. “The food industry makes products
with low profit margins. Unless a technology is affordable it
doesn’t stand the chance of being practically applied.”
The benefit here is also that metal surfaces (rather than
coatings) aremore robust and so using them inmarine biofoul-
ing environments is possible.
Some of these applications are already available. Anodic
NANOTECHNOLOGY