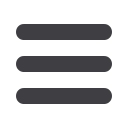

54
Wire & Cable ASIA – November/December 2014
www.read-wca.comFrom the Americas
between the June and July rulings, developers and analysts
said. The result was decreased demand for product from
some large, low-cost manufacturers – like Yingli and
Suntech, both Chinese – that had long dominated the
market.
But the higher prices were a boon to other companies,
in the USA and elsewhere, whose products were suddenly
seen as competitive, winning them new business.
Ms Cardwell and Mr Bradsher gave some examples of
activity in the revived sector:
Rooftop solar power provider SolarCity (San Mateo,
California) announced it would buy as much as
240 megawatts’ worth of panels from REC Solar,
a Norwegian manufacturer. It also acquired a start-up,
Silevo, with plans to produce panels in Buffalo,
New York.
SolarWorld Industries America, the Oregon–based unit
of Germany’s SolarWorld, is the manufacturing company
that brought the original trade case. It announced
a deal to sell equipment to RGS Energy (Boulder,
Colorado), an installer of power systems.
“We’re scrambling to buy modules with solar cells
made in Korea, Japan and Malaysia,” Ocean Yuan,
the president and founder of solar panel importer
Grape Solar (Eugene, Oregon), told the
Times
.
The reporters pointed out that the USA had already,
in 2012, imposed duties on solar panels made from
Chinese solar cells – the final major parts to be
assembled into modules. But many makers avoided the
duties by using cells produced elsewhere, especially in
Taiwan.
The current proceeding is part of an effort by
SolarWorld Industries America to close that loophole.
Indeed, the 25
th
July decision included Taiwanese
cells and imposed duties on them of 27.59 per cent to
44.18 per cent.
Of related interest . . .
The United States International Trade Commission
(USITC) on 6
th
August ruled out issuing any anti-dumping
and countervailing duty orders against certain categories
of steel threaded rod from India. The announcement
came a month after the US Department of Commerce
requested an investigation into Indian steel threaded rod
allegedly being sold in the United States at less than fair
value.
In July the Commerce Department determined that
imports of steel threaded rod from India had been sold
in the USA at dumping margins ranging from 16.74
per cent to 119.87 per cent, and that imports of the
material had received subsidies ranging from 8.61 per
cent to 39.46 per cent. But the USITC decided that the
domestic industry was neither materially injured nor
threatened with material injury by reason of the imports.
Imports of steel threaded rod from India into the USA in
2013 were valued at an estimated $19 million.
Technology
A study of wear in sliding metal parts
may hold key to damage prevention
during basic manufacturing processes
Wear is a major factor in metal failure during processing.
The discovery of a mechanism for wear in metals – swirling,
fluid-like microscopic behaviour in a solid piece of metal
sliding over another – holds promise for improving the
durability of metal parts in many applications.
The findings are the result of a collaboration of researchers
from Purdue University (West Lafayette, Indiana); M4
Sciences, a local company; and the Indian Institute of
Science, in Bangalore.
As described by Emil Venere, of Purdue, in
R&D Magazine
(formerly
Industrial Research
), the researchers, using a
microscope, high-speed camera, and other tools, had
previously observed the formation of bumps, folds, and
vortex-like features on sliding metal surfaces.
Building on that, they went on to link the behaviour to wear
in sliding metal systems. (“Discovery Is Key to Metal Wear in
Sliding Parts,” 24
th
July)
The team observed what happens when a wedge-shaped
piece of steel slides over a flat piece of aluminium or
copper – a common method for modelling the mechanical
behaviour of metals.
Tiny bumps formed at the leading edge, followed by the
swirling movement. As the wedge slid across the metal
specimen, folds formed between the bumps, crumbling into
tears and cracks in the wake of the wedge and eventually
falling off as wear particles.
“A single sliding pass is sufficient to damage the surface,
and subsequent passes result in the generation of
platelet-like wear particles,” said lead researcher Srinivasan
Chandrasekar, a Purdue professor of industrial engineering
and materials engineering.
The observed defects range in size from 5 to 25 microns
and are similar to those found in the sliding components
of parts for a variety of equipment and machinery including
automobile engines and compressors.
According to Dr Chandrasekar, they also occur in surfaces
created by grinding, polishing, burnishing, peening,
drawing, extrusion and rolling – basic manufacturing
processes in the wire and cable, ground transportation,
aerospace and energy systems sectors.
Future work at Purdue will explore how grain size and
ductility influence this type of metal wear, with the
goal of eliminating these surface defects through such
wear-control strategies as modified design of tools
and dies.
Dorothy Fabian
Features Editor