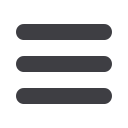

J
anuary
2008
www.read-tpt.com132
›
The application of quick change technology
to high precision tube mill operation
in a just-in-time environment
By Bruce Chidlow, senior tube mill operations engineer, Kusakabe Co Ltd, Japan
Introduction
Productivity and quality improvement is an unrelenting activity for all
organisations involved the manufacturing sector. Productivity and
quality are key performance indictors for any organisation today
and competition – both local and international – ensures it stays
that way.
In the tube and pipe industry, machine productivity is measured by
the following sample of indicators: tonnes or (metres) per hour and
percentage uptime. But in terms of quality there are more measures.
There is the amount of scrap in tonnes, dollars and percentage and
customer complaints issues expressed in number of incidents,
dollars and metres or tonnes. Of course, the overall measure is
conversion cost per tonne.
Understanding the current situation
It is important to establish a method to improve all of these
indicators year on year. There are many factors to consider
including management, labour, environment, systems, tools,
training, information, knowledge and equipment. This article will
concentrate on the equipment, information, knowledge and some
system factors.
To apply and fully utilise quick change technologies, it is best to fully
utilise the existing equipment and therefore fully understand the
shortcomings in the existing production environment. The tube mill
itself will be the focus of this article and not the surrounding support
systems.
A good method that will give an indication of where the problems
are, is to understand the downtime issues. It is vital to record and
track downtime percentages. Downtime is calculated by working
out the total time manned minus the mill run time, with the result
divided by the total time manned, and multiplied by 100 to get a
percentage. Reasons for downtime should also be collected, in
addition to the time lost and the number of occurrences. The cause
of the downtime will come later.
Conducting a Pareto analysis of the reasons for downtime will
highlight the items that need to be addressed. In accordance with
the Pareto principle, 20 per cent of the causes will account for 80
per cent of the downtime. Collecting good information can be a
problem. If this is being done for the first time the causes will be
very obvious. If this process has been going on for 5 years or more
then the quality of data collection becomes an important issue as all
the easy and obvious problems should have been solved. Collection
of accurate data will be covered latter in this article.
There will be some issues that will be difficult to overcome; they
usually stem from machine reliability and machine design issues.
They are a challenge but perseverance is required. These issues
need to be fully understood to make sure that the same mistakes
are not made on the next purchase or major modification.
Downtime analysis
Experience has shown that downtime can usually be separated into
two categories.
• Getting material to and from the mill
• Things that happen at the mill
Material supply and removal
Getting material to the mill and getting it away from the mill is
usually a larger problem than first imagined. Many mills run slower
than their rating to overcome these problems. The run speed then
becomes fixed and after a few years no-one knows why they run at
this speed. It is assumed that it is the limit of the mill.
In terms of equipment supply there are now many options that
enable large improvements in productivity by overcoming these
issues with the supply and removal of material from the mill.
There is no reason why a mill should be stopped or run at a slow
speed because the strip supply cannot keep up. Getting the steel
strip to the mill involves the use of cranes and/or forklift trucks,
double sided uncoilers, automatic coil loading systems, automatic
shear welders and strip accumulators (loopers). If space is an
issue then strip accumulators come in both horizontal and vertical
versions. This type of equipment is available for the smallest to the
largest tube and pipe mill.
Cost justification is usually straightforward for this type of equipment
as the increased uptime translates into increased volume and
increased sales or reduced overtime and labour costs, operating
costs and reduced scrap.
fi
Figure 1
:
Example of a tube mill downtime analysis – hours versus reason