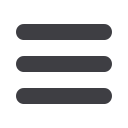

135
J
anuary
2008
www.read-tpt.com›
Case study
A low volume, high product mix tube mill operation (providing tube to
the automotive ride handling and exhaust sector) needed to reduce
the cost of its tube making operations. The operation had to make
120 different products and keep total stock levels below 6 days.
The mill had to be suitable to handle stainless steel 409 436,
aluminium coated mild steel, high tensile carbon steel and deep
draw quality carbon steel. The mill would have to handle 18
diameters between 36 and 60.5mm and 10 wall thicknesses from
0.8 to 3.2mm. These activities were undertaken and a project to
purchase a new tube mill line was developed and approved.
The existing tube mill was 50 years old with many modifications.
Reject levels were still high and productivity low. Both of these
indicators had improved tremendously over a two year period but
were still a long way from world class.
To meet the requirements of a just-in-time (JIT) environment, there
was a need for high quality and accurate tube where defects are
counted in parts per million. There was also the challenging task of
reducing the cost of manufacture.
Tube mill specifications
(quick change high quality tube mill)
The tube mill, that was specified and then met and surpassed the
targets, is described below.
1. An automatic double-sided vertical uncoiler that was loaded
using c hook and crane
2. Leveller to flatten the nose and tail of the coils (fully automatic)
3. Shear and welder TIG (fully automatic), hole punch for end
weld detection and mistake proofing
4. Strip accumulator to ensure the mill did not stop for end welds
5. Flying strip shear to minimise changeover times and scrap
6. Break down stands 1 and 2 where mounted on a turret to allow
for quick change and offline tooling setup
7. A cage was used to form the tube from the break downs to the
fin passes
8. Fin passes 1 and 2, fin pass side stand and the inverted 3
roll squeeze stand where mounted on a Turret similar to the
breakdowns. There was limited space for the installation and
the Turret provided the maximum utilisation of the space. No
seam guide was used
9. A solid state HF welder was installed. The repeatability of the
settings was critical for the stainless steel manufacture
10. A Pyrometer and squeeze pressure monitoring and feed back
control system was installed
11. SCADA system installed to track 16 variables at 1 second
intervals and also down load variables from the master data
base to the PLC
12. Internal fin cutting was installed with monitoring equipment
13. An ironing pass stand was installed to assist control the internal
fin cutting depth required to produce tubing for cylinder bore
product
14. Eddy current was installed after the cooling tunnel however its
use was discarded as other systems ensured that faults that
the eddy current could find were not produced
15. The sizing section consisted of a single Modular Sizing Mill
(MSM). This provided OD tolerance better that a conventional
mill. However, OD tolerance can be further improved by
adding additional MSM stands or a rotary sizing mill or some
combination of these technologies
16. A simple motorised turkshead was used as a straightening
stand
17. Ink jet printers were installed and linked to the master database
and the clocks synchronised with the one used by the SCADA
system. Tubing was continuously identified with date and
time to the second. Any faulty tube could then be tracked and
investigated with ease
18. A flying double shear type cut off was used. Due to the high
speed and short lengths. 100 metres per minute at 4 metres
19. The tube was then sorted automatically on the run out
conveyor
20. The internal swarf was removed used high pressure water and
then drained
21. The tube was then stacked into stillages and sent to the cutting
machines, storage or packing
22. The mill layout was such that the uncoiler’s station was next to
the mill operator’s station. This enabled either operator to run
both stations when the other was away on other duties.
The operation was very successful and met and exceeded all
expectations. The success of these types of projects is the result of
understanding what is required, what is possible, what is available
and working closely with the suppliers to get the desired result.
›
Figure 6
:
Quick change high quality mill for the automotive industry
Kusakabe Electric & Machinery Co Ltd
11-2, 2-chome, Murotani
Nishi-ku, 651-2241, Hyogo, Kobe, Japan
Tel
: +81 78 992 9100
Fax
: +81 78 992 9139
:
sales@kusakabe.comWebsite
:
www.kusakabe.com