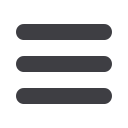

J
anuary
2008
www.read-tpt.com134
›
sides of the turret. The mill changeover consists of rotating
the turret through 90° or 180°.
5. There are also mills that use a combination of these
technologies. For example the quick change, high quality
(QHQ) mill that uses turret technology for the break down,
fin pass and squeeze stands. There is also cage forming to
move the strip from the breakdown to the fin passes and a
sub base system for the sizing section.
In all of these cases (except the flexible tooling), tooling is
changed and set ready for the next job offline. In the case of
flexible tooling the tooling is adjusted at the time of the job
change and is relatively fast using either power adjustment or
manual adjustment. This takes less time than that required to
change a sub base.
Converting other activities to outside work involves having enough
tooling to enable internal fin cutting and external fin cutting tools
to be set up offline. This ensures that all the mountings for this
equipment are of a quick change variety and that they always lock
into the same home position to minimise or eliminate the amount of
fine adjustment that is required.
Another area to consider is small improvements that add up. It
is important to minimise the number of screws and bolts and to
keep thread length to the minimum required to do the job. Where
possible, it is important to replace screws and bolts with quick action
clips and other quick change technologies.
Knowledge and Information
Another important aspect for efficient and low scrap changeovers is
knowledge and information. There are usually a very limited number
of employees on the mill that have a good solid knowledge base
about how to change over and set up the mill. This is very important
information that needs to be available to every one on the mill not a
limited few.
One of the best ways of doing this is to identify and list all of the
adjustments that exist on the mill from the entry to the exit. Each
adjustment must have a reliable and accurate setting method.
That is digital read out, scale or some other form of identification of
position. Data needs to be collected for each of these setting points
in relation to pipe OD, wt, length, tensile strength and strip width.
In most cases the relationships are very obvious but in others it is
more elusive. For each product produced a setting sheet can be
developed showing the tooling requirements and all the setting
points on the mill. The knowledge and information is now collected
and centralised and needs to be provided to all operators in a
standard form (ie set up sheets). The aim here is to make good
tube first time, every time. There is no point in changing the tooling
in 30 minutes if it take 60 minutes to make good tube. This also
eliminates the need for the next shift to reset the mill to meet their
personal preferences.
On all new equipment purchases it is important to ensure that all the
setting points can be adjusted easily, accurately and have indicators
to ensure the repeatability of settings. This also includes the welder
and ancillary equipment; basically everything that can influence
the product quality, repeatability of the set up and minimise the
production of scrap.
During this process it is important to note which items are critical
and can be monitored electronically. Collecting electronic data
using a SCADA system (usually on a 1 second interval) has
proved to be very beneficial in tracking quality issues when used
in conjunction with inkjet printed tube that has the manufacturing
time recorded on the tube. It is also a way of confirming if the
settings used to make the tube are the same as that on the set
up sheets.
Analysis tools and work environment
Analysis of downtime and the reasons for scrap start by being
reasonably simple in terms of the statistics and analysis tools used.
However, over time these tools need to be improved and upgraded
to ensure continuous improvement is achieved each and every
year; ultimately leading to a level equivalent to the internationally
recognised 6 sigma program.
It is extremely difficult for one person alone to achieve a highly
successful outcome, so team work, involvement and commitment
of all employees, staff and management is critical to ensuring a
successful outcome and an ongoing environment of continuous
improvement. This will always involve continuous culture change
and a continuously changing work environment.
It is important to ensure that all the effort and investment in the mill
is directed to achieve maximum benefit. The above methodology
goes a long way towards ensuring that this happens.
fi
Figure 4
:
Example of a setup sheet for the welding section of the mill
›
Figure 5
:
Example of SCADA tracking mill information