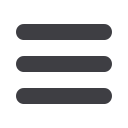

B
ending
, E
nd
F
orming
& S
waging
102
N
ovember
2009
www.read-tpt.com›
Ajax Tocco Magnethermic has combined
its knowledge of hardening oil pipe to API
standards with its pipe bending technology
to both bend and heat treat heavy wall
tube simultaneously. The process is for a
high specification 3" oil industry part, with
typical working pressure of 15,000 psi (test
22,500 psi).
Bending and hardening of heavy wall tube
Simultaneous pipe bending and heat
treating of heavy wall tube
A typical system is skid mounted and
includes the induction heating quenching
and bending equipment together with a
single operator control panel.
Ajax Tocco Magnethermic specialises in
the design and manufacture of ‘engineered’
induction systems to meet individual cus-
tomers' requirements. Investments include
extensive in-house heat treat facilities
complete with metallurgical laboratories,
enabling process development to meet spe-
cific requirements. FEA analysis is routinely
used to minimise development times.
Ajax Tocco Magnethermic Corp
– USA
Fax: +1 330 372 8608
Email:
info@ajaxtocco.comWebsite:
www.ajaxtocco.comHydroPro Inc, USA, manufactures
systems and tooling for hydro-forming or
swaging. The company’s equipment can full
depth expand a 400mm (15.75") expansion
zone in just a few more seconds than it
takes to expand a 40mm (1.57") zone.
The expansion pressure and dwell
times can be precisely set and controlled
to accommodate different tube material
characteristics, which is of particular use
when using tubes with high spring-back
properties such as titanium and super
duplex stainless steel.
HydroPro’s SleevePro system uses
hydroexpanding technology to expand
sleeves or liners inside damaged parent
tubes, to repair cracks or strengthen eroded
or corroded tubes. The BoilerPro system
mechanically sets and flares the ends of
boiler tubes prior to hydroexpanding or
mechanically rolling the joints.
The TubePro WeldLock system locks
the tube in the tubesheet, precisely sets
the tube protrusion and centres the tube
in the hole, while leaving small air gaps
that allow weld gases to escape during the
welding procedure. The TubePro WeldLock
tooling’s automatic centring process sets
the weld gap between the tube and the
tubesheet hole constant throughout 360°
of arc at the tubesheet face, in around six
seconds. This system eliminates the need
for tack welding, or lightly rolling tubes in
place to prevent movement prior to welding
or tube-to-tubesheet expansion. This is said
to enhance the quality and consistency of
the finished weld, whether performed with
automatic orbital welding equipment or by
manual welding methods.
HydroPro Inc
– USA
Fax: +1 573 732 3318
Email:
engineering@hpro.comWebsite:
www.hpro.comSwaging systems and tooling
HydroPro’s HPX 6000 base system
Tube cutting and
bevelling machine
The TT-NG series of portable and self-
centring tube cutting and bevelling
machines from Protem are designed to
perform accurate cutting and bevelling
works on tubes and pipes of all schedules
in one simultaneous operation, particularly
on tubes with large wall thicknesses.
The robust Protem TT clamshells can be
used in various positions and are suitable
for all types of materials. Their split frame
configuration allows the clamshells to be
opened in two half-shells. For manual
clamping, four independent adjustable jaws
are used.
The nine models in the series range
from the 45kg TT-NG 168 with a machining
capacity of 60.3-168.3mm (2"-6"), to the
205kg TT-NG 900 with a capacity of 660.4-
914.4mm (26"-36").
Protem SAS
– France
Fax: +33 4 75 57 41 49
Email:
contact@protem.frWebsite:
www.protem.frProtem GmbH
– Germany
Fax: +49 7247 9393 33
Email:
info@protem-gmbh.de
Protem’s portable TT machine in action