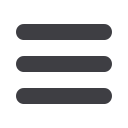

B
ending
, E
nd
F
orming
& S
waging
www.read-tpt.comN
ovember
2009
105
›
Manchester Tool & Die, Inc, USA,
offers Pines Technology Model 660 tube
and rod end-finishing machines for fast and
simultaneous de-burring, ID/OD chamfering,
and facing. There are two Model 660
variants, one manually operated and one air-
operated, for finishing up to 1,500 ends per
hour and 1,875 ends per hour, respectively.
The end-finishing machines can provide
cost savings by freeing lathes and other
machines on a wide range of work.
Model 660 can also increase production
and improve accuracy compared to abrasive
Dynobend BV, The Netherlands,
manufactures a wide range of bending
machines, specialising in custom-made
machines to meet customers’ requirements.
The company’s latest developments
focus on the possibilities for automation
in the bending process, for customers in
industries such as heating/cooling, furniture
and automotive.
Automation can range from automatic
loading to complete functioning production
cells.
In these production cells it is possible
to work with loading systems, weld seam
detection units, transfer units, robots,
cutting systems, drilling/punching and even
end-forming machines. Camera systems
are used for checking bend quality, and can
assist in creating a work cell with higher
output.
The company states that, providing
bending is the main process, it is able to
Custom-made bending machines
The FL 600 3D from Tube Tech Machinery
Srl, Italy, was designed for machining tubes
and structural profiles with a maximum
external diameter of 610mm and a maximum
length of 24,000mm.
The tri-dimensional system allows
operation on any point in a sphere space,
while movement along five interpolated axes,
with precision ball screws and linear motors,
ensures high dynamics and performance.
FL 600 3D is equipped with a double
tube loading system: one from bundle, which
allows the automatic loading of tubes with
round, square and rectangular section and a
loading capacity of 10,000kg, and one from
chain, which also enables the loading of open
section profiles. It is composed of V-shaped
supports: the chains move at variable speed,
according to the tube diameter and weight,
and are made to slide on bearings to prevent
noise and wear. The movements of the
piece along the working axis are ensured
by four self-centring mandrels, activated by
synchronised hydraulic cylinders.
A tempered and rectified precision helical
toothed rack activates the advance, operated
by brushless motor and precision reducer
withslack recovery system.Themandrelsare
designed to allow the machining of different
diameters and sections, with no change of
tools. An integrated floating system allows
the compensation for a piece’s uneven
straightness during machining, enabling
precision machining even on particularly
irregular tubes, and preventing dangerous
mechanical stress on the mandrels.
The plant is automatically controlled by
two CNC controls: one for the handling area
and the other for the laser working area
(Sphera). A third CNC control manages
and supervises the laser source. The three
computers are set to interact with one
another, with no need for human operation:
they automatically handle profile loading,
dimensional control, 3D laser machining
and discharge of the machined parts.
The software is simple and user-friendly,
and can be upgraded to include the handling
of lists of materials and stock.
Tube Tech Machinery Srl
– Italy
Fax: +39 030 7256333
Email:
info@tubetechmachinery.comWebsite:
www.tubetechmachinery.comTri-dimensional system with three CNC controls
complete any working cell. When suitable
machines are available, the company
buys them and integrates them into the
process. If the right machine cannot be
found, the company develops one to fit the
requirements. The bending machine in the
process is the master, meaning that the
Dynobend specialises in
custom-made machines
computer of the bending machine regulates
all the other processes.
Dynobend BV
– The Netherlands
Fax: +31 53 850 7731
Email:
info@dynobend.comWebsite:
www.dynobend.combelts and de-burring wheels. Changeovers are
easy and can be completed in minutes with
four sets of tools covering a
5
/
16
" to 2" diameter
range. Eight spindle speeds are available from
760 to 3,920 RPM, and the maximum stroke
is 1¼". The end-finishing machines are easy
to operate and offer a variety of accessory
equipment and tooling options.
Manchester Tool & Die, Inc
– USA
Fax: +1 260 982 4575
Email:
edegner@manchestertoolanddie.comWebsite:
www.manchestertoolanddie.comTube and rod end-finishing machine
The air-operated Model 660 end-finishing machine