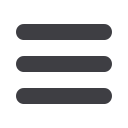

B
ending
, E
nd
F
orming
& S
waging
104
N
ovember
2009
www.read-tpt.com›
TUBE bending specialist Pines Technology
has announced a distribution agreement
with Gregson Induction Benders Ltd (UK),
which specialises in induction bending
solutions.
The companies said the transaction
will bring together two of the largest
global names in large tube manipulation
products and services.
Mr Ian Williamson, chief executive
officer of Pines said: “It will provide our
collective North American customer base
with technical solutions from us both,
while lowering our product costs for North
America.” He added: “This agreement
UNISON, UK, has launched an all-electric
tube bending machine that has the power
to bend tubing with outside diameters up to
170mm (6.7in).
The new Breeze 170 can generate a
bending torque as high as 135,000Nm
– which is nearly 50% more than the
company’s previous most powerful 150mm
machine. It brings the enormous process
flexibility and business advantages of
software-controlled set-up and bending to
a new class of heavy-duty applications.
The Breeze 170 is likely to open up
entirely new application areas in aerospace
and shipbuilding. The machine’s ability to
accommodate such large diameter tubing,
combined with its power and precision
bending capabilities, make it particularly
suitable for handling lightweight high-
strength ducting manufactured from
specialist materials such as commercially
pure CP titanium, titanium alloys and
stainless steel. Fast, software-controlled
setup enables the Breeze 170 to handle
batch sizes as small as one in a very
efficient manner.
The Breeze 170 offers highly accurate,
fully programmable control of the rotary
draw bending process. The machine can
accommodate tubing with a wall thickness
of up to 3mm and can produce bends of up
to 180 degrees, with a bending speed of up
to 10 degrees/second.
It can also perform bending operations
extremely slowly, which is a critical attribute
for the precision forming of titanium. The
Breeze 170 is designed specifically for
absolute rigidity, and uses fast-acting
closed-loop servo control to ensure very
US specialist signs distribution agreement
to supply large diameter bending solutions
Manufacturer launches powerful all-electric tube bending machine
confirms Pines strategic direction to
specialise in large bending applications.
The addition of Gregson Products to
Pines large draw benders means Pines
covers the complete range of pipe and
tube bending requirements for the power
generation, energy and petrochemical
industries”.
“Pines’ heavy duty CNC and NC
benders are exported competitively all
over the world including India and China.
Manufacturing the Gregson Induction
Benders in the US is therefore compelling.
We believe the future for Pines lies in large,
high value equipment either imported to
high process accuracy – the machine
provides a repeatability of ±0.1 degree on
both the bend angle and the bend plane.
Bending accuracy is further supported by
a unique wiper die system, which features
precision set-up facilities.
The Unibend machine control software
supplied with the Breeze 170 runs under
Windows XP or Vista on any industry-
standard PC. This software has evolved
steadily ever since Unison produced
the world’s first all-electric tube bending
machine in 1994, and is now widely
acknowledged to be one of the most
versatile tube-bending packages on the
market. Unlike traditional hydraulically-
powered tube benders, Unison’s all-electric
machines provide users with complete
control over the bend operation; they
can modify the bend speed, clamping
pressure, pressure die position and force,
and mandrel positioning parameters, to
achieve the optimum bend. Advanced
features include fully automated tube
sensing and clamping, which reduce setup
times significantly.
The software also includes powerful
remote diagnostic aids, which enable
Unison’s engineering team to quickly
resolve any bending problems or machine
performance issues at customers’ sites.
A software 'black box' – which
automatically stores the last 500
instructions entered by the operator,
together with details of machinery positions
from the servo motor sensors – allows
Unison to help its various users optimise
their processes, and to provide remote
maintenance services.
Pines specification or built in the US to
partner specifications such as Gregson.
Nigel Gregson, managing director
of Gregson Induction Benders Ltd
said: “Much like Gregson, Pines has
an enviable reputation for the quality of
its bending and tooling products, and a
willingness to provide the finest solutions.
The combination of Gregson and Pines
is extremely valuable as it will create
a powerful potential leader in the tube
bending industry with an enhanced,
complete products and services portfolio
second to none.”
Pines Technology
– USA
Fax: +1 440 835 5556
Email:
iwilliamson@pinestech.comWebsite:
www.pinestech.comTube bending operations can be
programmed in three ways. Programs can
be generated automatically, by transferring
data from CAD software files –Unison has
interfaces for all popular CAD packages,
and will develop interfaces for any others
that are required, including amanufacturer's
proprietary design software.
A simple programming template is
also available, enabling users to create a
program by entering the distance between
bends, the angle of bend required, and
rotation of the tube. A further option is
copying or reverse engineering, by using
a tube measuring system to recreate the
coordinates directly from a sample or
prototype.
In place of hydraulic force, the Breeze
170 employs servo motors to control the
entire tube bending process, including
clamp, pressure die, mandrel and follower.
This all-electric actuation provides
significant performance benefits in terms
of energy consumption, repeatability, and
noise reduction.
The actuation elements of the machine
only draw appreciable current when a
bend is being made, reducing energy
consumption significantly; at all other
times, the Breeze 170 consumes less than
1.5 kW/hour. Noise is also measurably
reduced – the Breeze 170 only generates
around 50-60 dB, which is equivalent to
normal voice level.
Unison Ltd
– UK
Fax: +44 17235 82379
Email:
enquiries@unisonltd.comWebsite:
www.unisonltd.com