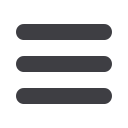

B
ending
, E
nd
F
orming
& S
waging
www.read-tpt.comN
ovember
2009
107
›
n
Ava-Matic UK has launched a machine
that features side loading of tools, which
eliminates the need for lifting equipment. The
AV65S is suited to small batch or prototype
production to high volume applications.
Conventional end-forming machines
have tool changes carried out by lifting
and dropping tooling in from a top
access. This requires the use of lifting
equipment, which can be awkward and
time consuming. The operator may need
to lift anything up to 27kg, which can be
hazardous and can contravene health
and safety regulations.
Other features of the AV65S include
a PLC that can run the machine in a
semi-automatic mode and store up to
300 machine settings. Typical production
times to expand a tube are 2 seconds,
and a claimed accuracy of ±0.02 can be
maintained.
Tooling for expansion and reduction
are all compatible with the existing
Ava-Matic range, and in most cases will
also accept other manufacturers’ tooling.
The practical, user-friendly design makes
use of work/storage platforms, and enables
tool changeovers to be performed quickly
and efficiently. The small footprint allows
the machine to be included as part of a
manufacturing cell or to be positioned in
areas of limited space.
The segmented tooling enables end-
forms to be produced on or near bends
without requiring any tube clamping. The
expansion or reduction of the tube is
infinitely adjustable with only a small range
of tooling to encompass tube sizes up to
153mm/6" diameter.
A wide range of expansion and reducing
tools is available off-the-shelf, and special/
bespoke tool designs can be supplied with
a short lead time.
Ava-Matic
– UK
Fax: +44 1527 518526
Email:
info@avamatic.co.ukWebsite:
www.avamatic.co.ukFabricom, Belgium, a manufacturer
of induction bends, has the advanced
technological and machine operating
capabilities required to produce pipe spools
with bends in multiple planes from a single
length of straight pipe.
This advanced bending technique is
the result of experience gained throughout
more than 30 years of manufacturing and
development work, and is of particular value
in onshore and offshore oil and gas pipeline
systems as well as specific applications in
the chemical, petrochemical and energy
sectors.
Some of the key benefits of producing
weldless pipe spools from straight pipes
are that it reduces the amount of welding
required, and as such the associated
costs and risks; and by reducing the
number of welds in the system, increases
plant integrity and safety while reducing
the required amount of in-service
inspection.
Fabricom operates six induction
bending machines with diameters of up
to 64", all of which offer a high degree
of flexibility in terms of bend radius,
bend angle and bend plane, and being
computer controlled, are able to achieve
close tolerances.
Optimisation of material properties
The company is able to work with all
types of material, including seamless or
welded pipes in carbon steel and stainless
steel, as well as the most sophisticated
alloy steels.
After bending, especially of heavy wall
materials or special alloy steels, it may
be necessary to restore the mechanical
properties using heat treatment. Such
treatments include stress relieving heat
treatment, normalising heat treatment,
normalising and tempering heat treatment,
quenching heat treatment, and quenching
and tempering heat treatment.
In order to be able to perform these
types of heat treatment, Fabricom has
five furnaces, all of which can be heated
to 1,200°C. In order to meet the strict
requirements set by the oil and gas industry
with regards to corrosion resistance and
superior material hardness, Fabricom also
has a quench tank at its facilities in Belgium.
Following heat treatment, bends can be
cooled down immediately in order to obtain
the right resistance and hardness.
Fabricom
– Belgium
Fax: +32 2 251 17 90
Email:
bending.be@fabricom-gdfsuez.comWebsite:
www.fabricom-gdfsuez.comMandrel tube
bending machine
technology
Langbow Limited, exclusive supplier of
Soco machinery to the UK fabrication and
manufacturing industry, offers the latest
development from Soco: DGT technology
(direct gear transmission).
Soco has secured the patent across all
major continents for the newDGT technology
for bending tubes and pipes. Using an
innovative system of power transmission
between the electric servomotor through the
bending shaft it is able to offer an efficient
power transfer method.
Soco has been developing tube cutting
systems since 1979, and its experience
with gear systems has provided it with the
background to research and develop a
suitable system for its CNC tube bending
range. By minimising the distance between
the electric servo and the bending shaft
(resulting in minimal loss in power) and
coupled with extreme low tolerance between
gears, Soco says that it has succeeded in
creating a durable and rigid system that
allows silent and precise tube bending.
Another advantage is found during the
tube push roll tube bending process. As
the tube must swiftly move through a set of
rollers, the smallest change and movement
on the bending arm may dramatically affect
the end product. The direct gear system
minimises such tolerances, bringing a stable
bend through the entire process.
The low noise level of the system
brings greater comfort to the operator
when using the tube bender, and meets
the requirements of various countries and
working environments.
The direct gear system is available over
a wide line of Soco CNC pipe benders,
including 3 to 12 axis models, with multi-
stack, variable radius and centreline
boosting options, together with Industrial
PC (IPC) interface and controls.
Langbow provides the full package in
support of Soco for the UK. This includes
purchasing advice, installation, training,
tooling support and unique five-year
warranty on all new Soco machines.
Soco Machinery Co, Ltd
– Taiwan
Fax: +886 4 23592386
Email:
info@soco.com.twWebsite:
www.socomachinery.comLangbow Limited
– UK
Fax: +44 1889 578872
Email:
sales@langbow.comWebsite:
www.langbow.comTube end former with side loading