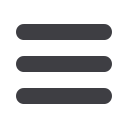

99
J
anuary
2009
www.read-tpt.com›
Designing tube mill rolls:
state-of-the-art software technology for
optimization of cage forming systems
By Mr Albert Sedlmaier, managing director, Data M Software, Germany,
and Mr Anton Skripkin, project engineer, CSoft, Russia
Introduction
The development of a new set of tube mill rolls and the following
production of accurate tubular sections might seem without serious
considerations. However, there can be problematic hurdles such as
down times of the tube mill, installation, startup and try-outs of roll
sets.
Internal strain and work hardening in the roll formed material might
cause poor welding conditions or deformation of the end-product.
For a number of years, data M Software GmbH, Germany, has been
offering a virtual process chain for the design and validation of roll
tooling for tube welding lines.
The Copra
®
RF (roll forming) software program family supports all
steps in the development of open or closed profile cross-sections.
This includes the design of the final cross-section to be produced,
the definition of the various shaping steps (passes or flower), and
the generation of technical documentation (ie production drawings,
parts lists, CNC programs), and later inline quality control of
profile cross-sections and roll tools. The latter works with optical
instruments developed especially for the application (Copra
®
RollScanner and Copra
®
LaserCheck).
This article describes how to perform a state-of-the-art roll tool
engineering for the production of longitudinally welded tubes.
It shows how to analyze and optimize a tube mill with integrated
straight edge forming stands using advanced finite element
computer simulation.
How to design tube forming rolls
on the computer?
In the past, the only way to create a properly functioning roll set was
through practical experience and extensive trials on the machine.
Today there is an alternative with effective design- and analysis
software, which speeds up this time-consuming and costly process.
Both the so-called ‘flower pattern’ and the roll tools are designed in
Copra’s tube mill software module.
The ‘flower pattern’ is the sequence of all subsequent tube forming
steps; it is very important to properly define the ‘flower patttern’
as it influences the final tube quality. The material is formed at
every roll station; this is the case not only for the intended
method with round tube but also in a longitudinal direction due
to the rollforming process. This can cause longitudinal strain and
may, if the material gets strained beyond its linear elastic limit,
inappropriately influence the material properties through effects
like local work hardening.
The principle of forming a strip into a tube in a tube welding line
is shown in picture 1. A special software program can be used to
determine the longitudinal strain values, taking into account the
influencing parameters defined by the roll tool layout.
The Copra
®
tube mill software module is a dialogue driven software
program that allows a parametric flower- and roll design for tube
mill rolls. It is important to know that the software does not stipulate
any specific tube mill or design strategy. It is completely free to
define any forming strategy the designer wants to develop and is
not restricted to any specific tube mill concept. This is important, as
there is no ‘global’ valid strategy for making tubes. The method to be
used always depends on the specific mill, material and tube data.
In a first step the user defines a certain tube mill and therefore
selects a number of standard forming stations from a catalogue
(picture 2).
Picture 1
:
Copra
®
DTM (deformation technology module) calculates longitudinal
plastic strain values resulting from the rollforming process in the tube mill
Picture 2
:
Mill definition in Copra
®
tube mill roll design software