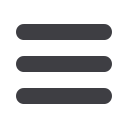

J
anuary
2009
www.read-tpt.com102
›
However, in some cases the tube forming process does not happen
as expected due to areas with reduced forming and punctiform force
distribution. Copra
®
FEA RF allows for a detailed evaluation of the
forming process in a rollforming line or a tube mill. This includes, of
course, the straight edge forming method.
The user is able to create and look at cross sections at any desired
position and compare between designed (intended) and simulated
(produced) cross sections. It is possible to check for strip edge
damages or waviness. An integrated report generator allows the
user to document discoveries and ideas by means of screen shots,
videos or comments in order to discuss these issues with colleagues
and customers.
The user also gets detailed information on stresses, strains and
forces occurring during the tube making process. It is possible
to evaluate any displacement of the formed strip and achieve
extremely important information about what is actually happening
in his tube mill. This possibility had previously been unfeasible. The
computer simulation allows the user to look ‘inside’ the mill and
extract respective information. This is impossible if a mill operator
has to do some troubleshooting on the tube mill without knowing
what is going on in the roll cage.
Another aspect that is decisive for a successful computer
simulation is the accuracy of the Copra EA RF software program
and the comparability of results with the real
production process. Various benchmarks performed
at the author’s company as well as some industrial
companies (tube producers, machine builders and
steel companies) are comfirming the high accuracy of
this software program.
A practical example
The objective is to investigate if a 24" tube can
be formed on a cage forming mill that is actually
designed to produce 20" tubes – and to determine
the achievable tube quality.
The material to be used is S355 (ST52) with a
minimum wall thickness of 7.5mm and maximum
of 21mm. The investigations described below were
performed on the minimum wall thickness as this is the most
sensitive dimension with regard to waviness effects. The maximum
wall thickness, however, was taken for a final verification of roll tool
adjustment and resulting forming forces.
A forming cage for such a 24" tube is usually not shorter than 12m.
However – as the cage available was limited to around 7m, several
investigations and trials have to be undertaken. The way to solve
such a project is carried out in some ‘optimization loops’.
It is essential to start with a certain design based on the
designer’s practical experience and analyze the forming process
by means of finite element computer simulation. This determines
any critical situation or material behavior. In this instance, it
was decided to determine the optimum alignment of the tube in
height. In other words, to define the optimum so-called downhill
strategy.
The target to achieve a 24" tube formed successfully on this mill
could be achieved. A linear downhill strategy would have been one
of the obvious solutions but was not possible due to the subsequent
fin passes following the roll cage that were aligned to a constant
tube bottom line. However, to predict the result, the distribution of
the final individual cross sectional lowering along the cage was
totally different. It is clear that any expert would have guessed this
from experience.
Picture 9
:
A feature of Copra is the possibility to design and model any type of rolling cage –
often referred to as straight edge forming method. Using this feature, respective rolls are not just
modeled but also transferred to Copra’s integrated finite element software package Copra
®
FEA
RF and simulated respectively
Picture 10
:
Automated creation of the FEA model by means of Copra FEA RF