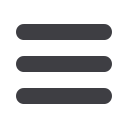

J
anuary
2009
www.read-tpt.com100
›
Picture 3
:
Selection of fine- or welding station during the definition of tube mill
stations (Copra tube mill software module)
Picture 4
:
Definition of the so-called ‘flower pattern’
Picture 5
:
Machine- and roll tool definition based on company specific standards
or from built-in formulas
chosen forming strategy. The decision whether to make use of the
single arc forming method or a double radius forming strategy can
be undertaken by a single mouse click.
The user can also compare the influence of different forming
methods in the break down stations like standard edge bending
versus W-forming – just by the press of a button (see pictures 6
and 7).
What is a cage forming system?
A comparatively new feature of Copra is the possibility to design
and model any type of rolling cage – often referred to as the straight
edge forming method. A cage forming system is a continuous
forming process by groups (beams) of single simple rolls and
additional supporting outer and inner roll tools.
This linear forming method can virtually be compared with ‘forming
a tube by pulling a sheet of paper through a funnel’, based on a
scenario where there is no entry and exit. Of course, steel does not
behave like paper.
It is necessary to enter a somewhat pre-formed tube into the ‘cage’
and retrieve the round but so far non-welded tube segment from the
cage and enter it into fin passes and welding stations. As a cage
forming system is no ‘funnel’, the number, size and position of all
the forming and supporting rolls have to be optimized as well.
A new way to determine the correct setup
parameters for a cage mill
Copra allows for a modeling of various types of straight edge
forming systems due to its parametric structure. The lineal beams
are either predefined or – if there are single mounted rolls – each
roll and respective position is defined in specific data base tables.
In order to achieve a proper forming result it is important to have a
smooth strip entry into the forming cage. Therefore it is important to
optimize both entry passes and the position of forming- and guiding
rolls in the forming line. Such tasks have to be undertaken by ‘trial
and error’ and are usually quite time consuming and pretty costly.
A straight edge forming cage for a large diameter mill can easily
reach a length of 12m or more – holding 4.5 to 10 tons of material.
The catalogue contains all standard types of roll tooling – from
forming stations down to the calibration passes. The user can
also modify each station according to specific requirements and
even include auxiliary tools like drawing dies or additional ‘forming
shoes’.
The proper forming strategy is defined by the design of the ‘flower
sequence’. This is nothing other than the actual knowhow of tube
making. At this stage all the angles, radii, length compensations,
dependencies, and additions for welding, calibration, and strip
guiding have to be defined. In addition, certain company specific
strategies or rules like ovalities have to be taken into account and
defined at this stage. In the Copra software respective values are
either calculated or taken from a number of tables. The user defines
both methods so every company can develop specific strategies
and store knowledge in the database for future use.
The definition of the tube welding line (machine) and respective roll
tooling method operate in the same way. Descriptive parameters
such as diameters, dependencies, relieve angles, and gaps, are
taken either from company specific tables or are calculated by
integrated formulas (picture 5).
Simple investigation of various
forming strategies
Both flower and rolls can be easily adapted by the parametric
system of the Copra tube mill design software. The user simply
changes either the values of respective forming angles or even the