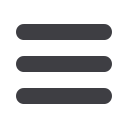

103
J
anuary
2009
www.read-tpt.com›
data M Software GmbH
– Germany
Fax
: +49 8024 640 300
:
datam@datam.deWebsite
:
www.datam.deCSoft
– Russia
Fax
: +7 495 913 2221
:
sales@csoft.ruWebsite
:
www.csoft.ru
Picture 15
:
Vertical cross sectional cut through the cage forming section. The
green arrow indicates the direction where the 90º bent tube tends to move
to. The blue arrow shows the route of the tube according to the cage roll
positions
Picture 11
:
Copra FEA RF allows for a detailed evaluation of the forming
process of the tube forming method – including straight edge system
In the first step, the flower pattern and respective roll tool design
was created (picture 12) and various downhill strategies were
investigated (picture 13, 14).
The following step was to verify each rollforming (tubemaking)
process and investigate the respective performances. It showed
that there were no optimum results from either the ‘linear downhill
strategy’ (or constant centre of gravity), or the strategy according to
minimized longitudinal strain values. The latter showed that these
processes do not match the ‘natural forming’ behaviour (which is
essential in the straight edge forming method due to high amount
of air bending), with regard to tube diameter, thicknesses, forming
length and material.
However, the ‘linear downhill’ method showed problems where the
tube leaves the cage forming section and enters the subsequent fin
stations. It was discovered that there was a constant bottom point
of tube profile.
Picture 15 clearly shows that this effect already starts within the
cage. The picture shows a vertical cross sectional FE drawing at a
position where the tube is already formed to a 90° angle. The tube
has already got such a stiffness that is cannot be pushed upward
any further in order to run smoothly into the following bottom roll
in the forming cage without getting damaged. Instead, the forming
was set to take place ‘on top’ by means of the upper rollers and a
kind of ‘free and natural’ bending, while the forming cage would be
aligned accordingly.
As a conclusion we ended up in a combination of both methods
– a linear downhill strategy in the beginning and a style of uphill
forming in the second part of the cage in order to achieve a smooth
and natural forming. It has to be pointed out that the bottom rolls
are supposed to bear only low forces and contribute to the forming
process in a minor way.
Picture 13
:
Downhill forming according to ‘minimum longitudinal strain’ values
Picture 12
:
The standard design of roll tooling with Copra (tube mill module,
cage design functions) with constant centre of gravity
Picture 14
:
Linear downhill forming method