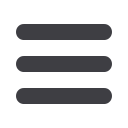

Technical article
July 2015
48
www.read-eurowire.comUltra-fast, high
resolution, surface quality
measurement (SQM),
for wires, optical fibres
and cables
By Jean-François Fardeau, Gérald Novel and David Miara, Cersa-MCI, R&D division, Cabries, France
Abstract
This project meets a long-time wire, cable
and fibre industry requirement for efficient
in-line surface quality measurement and
defect detection. It was recently allowed by
the very lastest technology progresses in
optoelectronics.
The system works like a ring linear camera
around the wires. The fine wire version
works from 10μm (0.4 mils) to 2mm
(80mils) in two models, fine and ultra-fine.
With 64 dots per circumference, about
300,000 circumferences per second (c/s),
and a dot size proportional to the wire
diameter, it brings surface detection
performance far above all present existing
technologies at a competitive cost.
It includes all necessary real-time electronic
computing: defect characterisation and
selection, and alarms. It connects to
external computers for data logging,
parameter setting, and image display
of the surface on PC screen, statistic
computing, production quality reports and
maintenance. (International patent July
2004). Other models, for larger diameters
and higher resolutions but lower speed will
follow by next year.
Introduction
In applications where surface quality
(roughness, flaw, lump, neck) is critical,
like special fine stainless steel wires,
gold wires and wire plating, coatings or
colourings of optical fibres, enamelling
of copper wires, broadband cables, there
was no instrument for high resolution and
high-speed whole-surface analysis.
The existing surface quality instruments
are based on standard camera image
analysis. The limits for fine wire are
the resolution on the wire, the image
frequency, and the lighting system for
surface analysis.
With the non-contact full circumference
imaging, this covers all the surface of the
wire at high resolution and high speed. It
becomes possible to evaluate the surface
and shape of the defect. At 300,000
circumferences per second and 64 dots
per circumference, at line speed of 30m/s
(1,800m/min) the axial resolution (pitch)
would be 0.1mm (4 mils).
Including the wire feed pulses for wire
length and speed measuring, the two
dimensions are known: length and
circumference.
That gives a two-axis image of the wire for
defect characterisation. Connected to a PC,
this can display local images of the wire
surface, especially when there is a defect,
for analysis and knowledge.
Using only static components, lifetime is
not a problem. Maintenance of optical
systems in harsh environments requires
specific care.
For low maintenance action, it uses clean
air pressure to avoid dust, vapour or
particles deposition on the inner glass tube
interface.
Principle
The idea came from the gleam of a
spotlight on a cylinder.
In this image, re/D is about two per cent.
Then re/π*D < 1% of the circumference.
The size of the gleam depends on the size
of the spot source and on the angular
aperture of the observer (optic of the
sensor).
The energy gleamed to the observer
(sensor) is strongly modulated by the
surface
quality;
roughness,
colour
(absorption) and flaw, but also the local
shape of the cylinder. Then, rotating the
light around the wire axis will also rotate
the gleam on the surface referring to a
fixed observer.
This generates a circumference image.
When the wire moves, it develops a
complete surface image of the wire. If the
design is well made, any small surface
defect, colour or shape change will
produce locally a significant reduction of
the gleamed energy to the sensor.
Entrance side Exit side
▲
▲
Figure 1