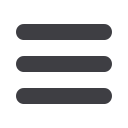

EuroWire – Luglio 2008
89
articolo tecnico
ad elevata resistenza alla cavitazione
combinato con un rivestimento secondario
che consenta un rilassamento degli sforzi
più rapido.
2.1.2 Formazione di cavità nel rivestimento
primario.
La
Figura 4
mostra delle immagini
al microscopio di alcune cavità formatesi in
una fibra rivestita con diametro esterno di
500 μm, dopo una variazione ciclica della
temperatura fra 85ºC e -60ºC. Si possono
osservare rotture del rivestimento di forma
irregolare di varie dimensioni nello strato
di rivestimento primario. La presenza di
rotture del rivestimento ben aperte, sotto
forma di vuoti, indica l’esistenza di sforzi
di trazione triassiale nello strato primario a
temperatura ambiente.
Per la teoria della meccanica della frattura,
si definisce resistenza alla cavitazione il
parametro che rappresenta tale resistenza
in un materiale. Quando uno sforzo
triassiale raggiunge questo punto critico,
il materiale inizia a rompersi e a formare
cavità interne. É stato calcolato e provato
sperimentalmente che per una gomma
ideale, lo sforzo triassiale per allargare
un foro sferico molto piccolo è pari a
(5/6)E, dove E rappresenta il modulo di
Young.
[6]
Qualsiasi difetto di reticolazione
microscopico nel materiale può costituire
il punto di rottura iniziale. Ciò significa
che, per un rivestimento primario di 1MPa,
uno sforzo di trazione triassiale di 0,83MPa
può già causare la formazione di cavità
secondo il meccanismo di crescita illimitata,
qualora il materiale di rivestimento si
comporti come una gomma ideale. Con
un’appropriata progettazione molecolare
della struttura reticolata del rivestimento,
si può ottenere l’elevata resistenza alla
cavitazione desiderata, con valori che
superano in modo significativo il modulo
del rivestimento.
In questo tipo di rivestimento primario ad
elevata resistenza alla cavitazione, le piccole
cavità non cresceranno illimitatamente
ed il materiale non si romperà nemmeno
nel caso di valori di sforzo di trazione
relativamente alti nel rivestimento primario.
2.2 Cavità indotte da sollecitazioni
meccaniche
Oltre allo sforzo idrostatico e termico,
la formazione di cavità nei rivestimenti
primari può essere causata anche da
sforzi triassiali anisotropici risultanti da un
impatto meccanico nella fibra rivestita.
Durante alcuni test di resistenza del
rivestimento alla delaminazione, realizzati
tirando la fibra attraverso un sistema di
riavvolgimento, è stato osservato che il
rivestimento si strappa se sottoposto a
tensioni elevate.
[4]
Quando si applica una forza meccanica
esterna ad una fibra rivestita, gli strati di
rivestimento si deformano generando
un campo di sforzo non uniforme nel
materiale di rivestimento. La
Figura 5
illustra schematicamente la deformazione
degli strati di rivestimento sottoposti ad
una forza laterale F. Poiché il rivestimento
secondario è costituito da un materiale
molto più rigido del rivestimento primario,
lo strato secondario si comporta come
un tubo vuoto, sottoposto a pressione
laterale, che passa dalla forma tubolare ad
una forma ovale, ma senza che lo spessore
del rivestimento si deformi. Il rivestimento
primario è fissato da entrambi i lati al
vetro ed al rivestimento secondario, ed
è forzato a deformarsi internamente. Le
aree del rivestimento primario lungo la
direzione della forza sono compresse, e
le aree perpendicolari alla direzione della
forza sono sottoposte ad allungamento.
Lo sforzo di trazione in queste aree
sottoposte ad allungamento presenta una
componente triassiale significativa che
può causare cavitazione del rivestimento
primario qualora lo sforzo superi la
resistenza alla cavitazione del rivestimento.
La
Figura 6
evidenzia un campo di sforzo
normale
medio
calcolato
mediante
l’Analisi ad Elementi Finiti nello strato di
rivestimento primario di una fibra con
una geometria del diametro esterno di
125/240/410 μm, sottoposta ad una forza
laterale simulata.
Il risultato mostra quantitativamente i
diversi campi di sforzo che variano dallo
sforzo di compressione (-) allo sforzo di
trazione (+). Come illustrato dalla
Figura 6
,
le aree sottoposte allo sforzo di trazione
maggiore sono i punti perpendicolari alla
direzione della forza applicata e vicino
ad entrambi i lati delle interfacce fra il
vetro ed il rivestimento primario, e fra il
rivestimento primario ed il rivestimento
secondario. Queste sono le aree ove la
cavitazione presenta maggiore probabilità
di iniziare a manifestarsi quando viene
applicata una forza meccanica laterale.
La
Figura 7
mostra qualche esempio
di cavità indotte intenzionalmente nel
rivestimento primario, causate da impatti
laterali meccanici. La forza laterale
deve essere dinamica con la velocità,
o longitudinalmente (scivolamento) o
perpendicolarmente (colpo). Una forza
laterale statica può condurre solo a
delaminazione. Nella
Figura 7
, l’impatto
meccanico è stato creato facendo
scivolare una barra metallica del diametro
di 1mm longitudinalmente rispetto alla
fibra. Con un’apparecchiatura realizzata
attaccando la barra di metallo ad un
tester di sfregamento automatico, sono
state applicate velocità controllate e
forze controllate aggiungendo vari pesi
alla stessa. Sia la forza, sia la velocità
d’impatto influenzano lo sforzo indotto
nel rivestimento. A velocità molto basse,
si produce delaminazione piuttosto
che cavitazione del rivestimento. Ciò
può accadere poiché la ridotta area di
delaminazione che si forma al contatto
iniziale con la forza, si propaga lungo
la fibra rilasciando lo sforzo di trazione
nel rivestimento. Come illustrato nella
Figura 7
, le cavità e/o la delaminazione
possono generarsi da medie ad alte
velocità. Le cavità sono localizzate nelle
due aree laterali, in accordo con la teoria.
Cavità e delaminazione sono due moda-
lità di errore in concorrenza. Possono
essere presenti individualmente o contem-
poraneamente, secondo le caratteristiche
di adesione e la resistenza alla cavitazione
Figura 7
▼
▼
:
Esempi di formazione di cavità/delaminazione nel rivestimento primario causate da impatti meccanici
laterali
Figura 8
▼
▼
:
Preparazione del campione per la prova di resistenza alla cavitazione
Placca di vetro
Resina (100 μm )
Barra di quarzo