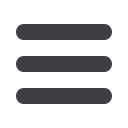

M
arch
2009
www.read-tpt.com108
›
New solutions for simulation of
hot and cold tube rolling processes
Mr A Vydrin, OJSC RosNITI, Russia
Introduction
The issues of plasticity in metal working simulation have long
attracted the attention of researchers. Simulations are divided into
physical and mathematical, with computer simulation considered
a modern form of the latter. The theoretical foundations for
mathematical simulation of rolling processes were laid in the second
half of the 20th century. This was the period when the majority of
calculation formulas were obtained based on the fundamental laws
of physics, but with a number of assumptions and simplifications to
ensure analytical solutions.
The end of the 20th and the beginning of the 21st century saw
the development of computer technology and the new methods of
numerical mathematics. Universal application software packages
were developed, including Deform, Ansys, Copra, Forge3, and Marc,
that allow numerical simulations of stress-strain and temperature
conditions of metal during its plastic working phase.
However, many researchers agree that the application history of
this software used by technologists and laboratory staff shows its
ineffectiveness in plant conditions. The reason behind it is laborious
preparation of source data and long a time (up to one day or longer),
required for the computing of one option, which effectively turns it
into a research project.
On the other hand, the use of analytical relations for technological
calculations does not always produce sufficiently reliable results
that will not require further technological development in plant
conditions. The two main reasons for this are as follows:
• A wide range of steel grades and sizes leads to the excessive
laboriousness of technological parameter calculations for each
combination of grade, type and size
• In a comprehensive approach, the task is usually described by
a set of nonlinear algebraic equations that are difficult to solve
without using numerical method and computers.
Nowadays in the area of plastic metal working simulation, particularly
in tube and pipe manufacturing, there are a limited amount of
software tools for implementing modern calculating methods that
base on analytical relations of plastic metal working processes.
Currently, OJSC RosNITI is developing a comprehensive approach
to the issues of simulation that will encompass virtually all research
trends and types of simulation.
The use of turnkey application program
packages
The solution of production problems (eg those connected with metal
forming), requires dealing with a hypotheses of the physical nature,
which in most cases involves correctness that can only be proved
with the help of computer simulation. The software system Deform-
3D is used for this purpose in cooperation with the Department of
Plastic Metal Working of Yuzhno-Uralsky State University.
Defining the strained condition of the plate edge when forming
helical-seam pipes is one of the tasks that can be solved with
the assistance of software. The simulation results have proved
the existing hypothesis on the origins of ‘bamboo’ flaw (figure 1)
observed in the formed pipe weld seam area.
Practice has shown that the application CosmosWorks, part of the
SolidWorks system, is an effective tool for simulation of structural
components of the equipment working in the elastic stress zone.
The use of this application is advisable for the performance analysis
of complex configuration non-standard equipment when the existing
analytical methods cannot be used without serious simplifications
and assumptions. This software was also used to analyse strength
Figure 1
:
Stress condition pattern in cylinder shaping
Figure 2
:
Stress condition
pattern of the
tube reducing
mill of a new
design