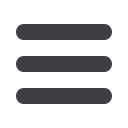

M
arch
2009
www.read-tpt.com110
›
If the new hypothesis is used in the basic set of continuum mechanics
equations, the multiplier
will be replaced with
where
s
s
0
is a free term of the linearized rheological equation.
A numerical simulation of the stress-strain state
On the basis of the setting problem of the refined continuum
mechanics boundary-value, the object-oriented simulator and the
numerical analysis software program for the hot tube reducing
process were created. The use of this software is more convenient
than the use of Deform, Marc and similar packages due to its
comparatively narrow application.
First of all, it is connected with the program-protected grid for
splitting the deformation centre into finite elements (figure 4) and
the minimal primary data input volume. The programme is primarily
aimed at the analysis of the tube metal forming to define, for
instance, limit values of frequent deformations that do not lead to
appearance of internal surface facets.
Design and application of tube deformation
process models
As was previously mentioned, there is a lack of software tools for
computerized calculation of manufacturing process parameters,
especially with an integrated description. As a result, a number of
programs have been designed in the Borland Delphi integrated
environment that can be used by production managers in plant
conditions.
One of these software products is a program for calculating
speed behaviour as well as energy and power parameters of the
hot reducing process. This software was designed for a specific
reducing mill at Volzhskiy Tube Works and so its database has a
maximum amount of information about this particular mill. For
instance, databases that can be corrected (if required) contain
information about the working stand inventory, pass parameters
and reduction schedules.
Due to the existence of databases for reducing speed calculations,
it is enough to enter dimensions of a finished tube and rheological
coefficients of the worked metal. The results can be represented
both in the form of tables, which is more customary to the plant
staff, and in the form of graphs. The application of this software
program in the plant conditions has enabled a dramatic reduction
of the number of adjusted tubes. It has also established the reasons
behind the diameter of thick-walled pipes being in the positive area
of the tolerance field.
Nevertheless, a significant influence of the tube diameter on
speed was noticed during the simulation process (figure 5). The
influence of pipe wall thickness on energy power parameters of
the process were also studied (figure 6). Along with the software
for the reducing mill setting, a software product for computerized
development of the tube reducing technology was developed. This
product is of a multipurpose nature and allows the development of
reducing technology for two- and three-roll stands, with or without
tension between the stands. An interface between the user and the
computer is also possible and it allows the introduction of changes
during the work with the program.
The technological para-
meters necessary to
receive tubes of the
target size and require-
ments are presented in
the table form. Figure 7
shows an example task
window that requires
a minimal quantity of
initial information for the
program operation.
Figure 5
:
The dependence of the reducing mill roll rpm on the tube diameter
Figure 6
:
The dependence of the force acting on rollers on the wall thickness of
reduced tubes
Figure 4
:
Deformation zone diagram in the tube reducing process
Figure 7
:
Task window of the automated design
programme for the pipe reducing technology