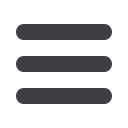

111
M
arch
2009
www.read-tpt.com›
The technological model is created for computerized development
of tool designs for cold tube rolling mills of KhPT and KhPTR types.
The model allows calculating of the calibration by three techniques,
each of which has its ideal application area depending on plastic
properties of the tube metal.
The program also includes databases that contain mechanical
properties of the steel grades used as well as the information on
technical reference documentation for cold worked tubes. This
design was successfully tested at KhPT-32, KhPT-55 and KhPT-75
mills at Sinara Tube Works. Figure 8 shows the appearance of the
information obtained.
Physical simulation of production processes
Mathematical simulation is not possible without using physical
simulation results; it is only possible to obtain the information about
the mechanical properties of metals and the boundary conditions
of the working process with the help of physical experiments. To
generate the information on the metal resistance to deformation
and other physical data, OJSC RosNITI works in close cooperation
with Department of Plastic Metal Working of Yuzhno-Uralsk State
University, whose research laboratory is equipped with a unique
cam plastometer.
The main advantage of this plastometer is the possibility to perform
fractional deformation that allows the simulation of continuous tube
rolling processes and the study of metal softening patterns between
passes. Besides, a special container design allows the performance
of simulation at a fixed specimen temperature.
Figure 9 shows the schematic diagram of the cam plastometer.
The possibility of a fractional specimen loading provided by the
plastometer allows the development and successful implementation
of the experimental research procedure of the resistance of metals
and alloys to deformation. It also reveals plastic deformation during
experiments excluding errors due to the contact friction during
plastic deformation. Furthermore, the process of physical simulation
is facilitated with the help of the computerized system for collecting,
converting and computer processing of data attached to the
plastometer.
The equipment for isothermal compressive deformation has allowed
the development of the procedure to determine friction coefficient
in hot and cold working. The method is based on the known
solution of the variational problem of cylinder yielding. The idea of
the method is yielding a cylinder specimen at the plastometer at
a predetermined temperature while observing the condition of the
specimen contact surface with the working tool. This is undertaken
by measuring the specimen contact surface diameter after yielding
with the help of a toolmaker’s microscope and computer processing
of the obtained data using a simulator.
In order to calculate parameters of the cylindrical specimen surface
stress-strain state during yielding, the solution of the variational
problem of cylinder yielding was further developed. This allowed
the considerable increase of the accuracy of determining metal and
alloy plasticity via physical simulation using the cam plastometer.
Conclusion
The effectiveness of the simulation methods used for research and
advancement of the tube rolling processes is determined by their
multipurpose application. All simulation (mathematical, physical and
computerized) methods shall be used to obtain reliable information.
The accuracy of setting the boundary-value problem, taking into
account its end implementation, has to be ensured to receive
reliable results when using mathematical simulation. In the case of
computer simulation, in addition to the use of available programs
it is advisable to create object-oriented programs. This is because
the application of such programs is more convenient for solving
practical tasks despite a somewhat limited application area.
The development of new computerized analysis procedures for the
production processes based on the known analytical solutions can
be recommended for an on the spot solution of specific production
issues. The implementation of new research procedures for
obtaining new kinds of information using the existing laboratory
equipment is reliant upon the development of an advanced trend of
physical simulation methods.
Bibliography:
1. VG Dukmasov, AV Vydrin ‘Simulators and the processes of high-quality flank
rolling’ – Cheliabinsk: YuUrSU Publishers, 2002 (p215).
2. VL Kolmogorov ‘The mechanics of metal plastic working’ – Moscow: Metallurgia
Publishers, 1986 – p688.
3. VL Kolmogorov, SI Parshakov, SP Burkin, Yu N Loginov et al ‘Plastic metal
working technological tasks solution using microcomputer’ – Moscow:
Metallurgia Publishers, 1993 – p320.
OJSC RosNITI
– Russia
Fax
: +7 351 734 70 60
:
maltsevpa@mail.ruWebsite
:
www.rosniti.ru
Figure 9
:
Schematic diagram of the
cam plastomter designed by YuUrSU
Figure 8
:
The results of computerized design programme for cold tube rolling
mill tool design