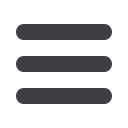

109
M
arch
2009
www.read-tpt.com›
and toughness of the non-standard design reducing mill stand
containing two pairs of working rolls separated by a minimal
distance (figure 2).
The design of theoretical aspects of
mathematical simulation using
numerical methods
OJSC RosNITI not only uses turnkey software tools but also
designs its own software products for the analysis of deformation
processes in tube and pipe manufacturing. The simulation process
of the stress-strain state is based on a set of continuum mechanics
equations.
Despite the fact that the basic continuum mechanics equations
have been developed more than a century ago, modern numerical
methods require their corresponding adaptation at the stage of
task description. Thus, to receive the approximate solution, the set
of differential equations of continuum mechanics boundary-value
problem has to be linearized.
The analysis has shown that the problem of linearization can be
solved when the approximate solution is made by the finite-element
method. In this case the basic set of equations is as follows:
Where
T
is shear stress intensity, determined with the help of
rheological relations;
H
is shear deformation speed intensity;
v
i
is
speed vector components ;
s
is average normal strain. As the final
element (
e
) takes a small volume, the relation
T
/
H
within its limits
can be considered constant regardless of the complexity of metal
rheological characteristic and it ensures linearization of continuum
mechanics boundary-value problem.
It is possible to undertake theoretical analysis of the projection
method algorithm of boundary-value problems. The approximate
solution has shown that the generalised form of recording boundary
conditions for the case under review is as follows:
In this case,
G(M)
is the known function given at point at the
boundary of deformation centre
S
. If the function
G(M)
is selected
properly, the generalized boundary condition is reduced to the
known kinds of boundary conditions of plastic metal working
theory
[2]
.
The calculation accuracy of the stress-strain state in many respects
depends on the accuracy of rheological description of the continuum
in the numerical solution of a boundary-value problem. To linearize
the set of continuum mechanics equations, the rheological relations
also need to be linearized. The accuracy of this operation, in turn,
determines the correctness of the task solution.
Currently linearization is usually performed by AA Iliushin's method
of variable elasticity. This method takes into consideration the
physical equations of the connection between stress and strain
conditions that are formulated based on the hypothesis that deviator
components of strain and deformation speed tensors are directly
proportional.
However, in this case the straight lines that linearize rheological
relations at each step always go through a grade level which
results in a sawtooth nature of linearized rheological relation in
the deformation centre volume (figure 3a). For a more correct
record of metal rheology, it is suggested that the formulation of the
connection between stress and strain equations has to be based on
the hypothesis about the linear dependence between the deviator
components of strain and the deformation speed tensors. This
situation is depicted in the following:
s
ij
=
s
ij
0
+ ke
ij
'
In this instance,
s
ij
and
e
ij
are deviator components of strain and
deformation speed tensors;
s
ij
is a free term.
Application of this hypothesis allows the achievement of a
considerably smoother rheological curve (figure 3b) and an increase
in the accuracy of the boundary-value problem solution. At the
same time, it is easy to notice that when setting
s
ij
0
= 0
we arrive
at the existing hypothesis that formed the basis of the formulating
equations that show the connection between stress and strain
conditions.
Figure 3
:
The ways of
rheological
relations
linearisation