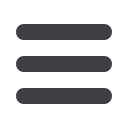

Technischer artikel
September 2012
76
www.read-eurowire.com▲
▲
Bild 5
:
Linke Seite –
∆
E berechnet von den Angaben im Bild 4 (mit Sollwerten 87,62 / -66,04 / 39,10)
Rechte Seite – Histogramm von
∆
E mit einer Klasseneinteilung von 0,05. Durchschnittswert
∆
E = 0,89
▲
▲
Bild 6
:
Zwangsfarbfehler durch Einfügen von Blau-Masterbatch in die Trommelversorgung
▲
▲
Bild 7
:
Rohangaben mit Streifen – gut erkennbare Änderungen im a*- und b*-Kanal wenn der Streifen sich durch
das Scan-Feld bewegt
Prüfung mit 1 Farbe (gelb)
Verteilung von dE
(Klasseneinteilung = 0,05)
Abtastzeit [min]
d
E [AU]
Position in der Kugel unabhängig. Oder
anders gesagt: das Lab-Modell ist eine
mathematische Beschreibung der vom
menschlichen
Auge
interpretierten
Farbunterschiede, das immer gleich
ist unabhängig davon welche Farbe
verglichen wird.
Statistische Prüfungen basierend auf
CIE-Lab haben gezeigt, dass
∆
E-Werte
über 10 vom Menschen als wesentliche
Farbabweichung
betrachtet
werden,
viele Menschen können Farben bis zu
∆
E≈4 unterscheiden. Nur sehr wenige
davon können mit sehr gut trainierten
Augen Unterschiede zwischen 2 ≤
∆
E
≤ 4 sehen. Untere
∆
E≈2, unterscheiden
die Rezeptoren nur eine einzige Farbe.
Ein weiteres Problem ist (teilweise)
Farbblindheit.
Tabelle 1
ist von Studien
unter Bevölkerungsgruppen industrieller
Länder entnommen (z.B.
[4]
) und zeigt,
dass fünf Prozent der Männer eine
Grünschwäche
(Deuteranomalie)
aufweisen, und daher sind sie schwach im
Erkennen geringer Farbtonunterschiede.
Nur mit einer objektiven automatischen
Farbkontrolle können Fehler vermieden
werden die dadurch verursacht werden.
Technische
Anforderungen und
Probleme, die durch
die Drahtgeometrie
und -verarbeitung
verursacht werden
Farbmessung
basierend
auf
CIE-Lab
ist
heute
Stand
der
Technik in der Lackindustrie oder
bei
Graphikanwendungen,
mit
Toleranzwerten, die manchmal
∆
E <1
entsprechen. Die Voraussetzungen für
derart genaue Messungen sind flache
Gegenstände, ein Scanpunkt mit einem
Durchmesser von zirka 5-10mm und
eine Abtastzeit von ungefähr 100ms auf
einen bewegungslosen Gegenstand –
aber all diese Voraussetzungen sind bei
einer Extrusionslinie bestimmt nicht
gegeben. Deswegen müssen bei einer
Inline-Abmessung nachfolgende Punkte
berücksichtigt werden:
• Mit
einer
sehr
kurzen
Abtastzeit beseitigt eine Durch-
schnittsberechnung
über
eine
bestimmte Anzahl an einzelnen
Aufnahmen,
die
örtlichen
Abweichungen. Das kann dadurch
begründet
werden,
dass
die
Farbwechsel bei der Extrusion eine
relativ lange Übergangszeit aufweisen,
die durch die Mischwirkungen im Fass
verursacht werden
• Die
Gegenstandbewegung
(Jitter)
muss bei der Sensorstelle minimiert
werden. Das ist wichtig für den
Gegenstand-Sensor-Abstand d
s
(die
Beleuchtung reduziert sich mit d
s
2
)
sowie für die Querbewegung, wo der
Gegenstand den Scanpunkt teilweise
oder völlig verlässt
• Die
Drahtgeometrie
wird
als
Seitenansicht
auf
einer
Zylinderoberfläche erfasst. Daraus
resultiert eine Farbvariation von
der
Ansicht
der
Zylindermitte
zum Zylinderrand. Diese Wirkung
wird
zusätzlich
durch
die
Oberflächenrauheit beeinflusst.
d
E [AU]
Masterbatch-Mangel vom Trichter
(Blaukorn)
L*, a*, b* [AU]
Prüfung mit Doppelfarbe (blau-grün) [AU]
Gelbisoliertes Kabel mit Masterbatch-Mangel vom Trichter (Blaukorn)
Zeit (s)
d
E [L*a*b*]