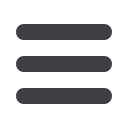

Technischer artikel
September 2012
77
www.read-eurowire.com▲
▲
Bild 8
:
Prüfung des Streifenmangels – nur beim a*- und b*-Kanal ersichtlich. Der Co-Extruder wurde ausgeschaltet
bei der x-Meßstabposition 10s und wieder eingeschaltet bei Position 50s
▲
▲
Bild 9
:
Benutzerschnittstelle der Farbmessung. In der oberen Mitte zeigt ein schematischer Querschnitt des Drahts
die erfasste Haupt- und Streifenfarbe. Die untere Mitte zeigt den zur SPS übermittelten Zustand (grün = beide Farben
in Toleranz, gelb = eine fehlt oder ist außerhalb der Toleranz, rot = Doppelfehler oder falsches Rezept). Auf der
rechten Seite wird die Information über die aktuelle Farbe angezeigt
▼
▼
Bild 10
:
Prototyp des Siebe-Farbmessungssystem
während der Prüfung bei der Linie eines
Kunden. Installation zwischen Funkprüfung und
Knotenwächter-Kamera. IPC am Ober-, Unter-,
Drehmechanismus und Sensor (unter Lichthülle)
Da beide Bedingungen nicht geändert
werden können, kann der Wert der
Endfarbe nicht als absolute Messung
interpretiert
werden
sondern
als relative Messung mit hoher
Reproduzierbarkeit
In
der
Regel
läuft
eine
Linie
mit
unterschiedlichen
Leiter-/
Isolierungsdurchmessern.
Diese
Vorrichtung sollte mit verschiedenen
Geometrien
funktionieren
können
(innerhalb einer bestimmten Auswahl)
ohne mechanische Vorbereitung oder
Nachkalibrierung der Sensoren.
Eine weitere Herausforderung liegt in der
Messung bei der Produktion farbkodierter
Drähte (ein oder zwei Streifen). Da die
Endfarbe sich nach der Abkühlung des
Polymers festsetzt, hat die Probenahme
nach der Kühlwanne zu erfolgen. Wegen
der Umlenkräder und desselben Produkts
(insbesondere bei verseilten Leitern), kann
sich der Draht auf unregelmäßiger Weise
um die Längsachse drehen. Daher erfasst
der Sensor manchmal die Hauptfarbe,
manchmal die Streifenfarbe, oder beide
gleichzeitig im Scan-Feld.
Bild 3
stellt ein
Bild aus Sensor-Sicht eines zweifarbigen
Drahts dar. Mit einer hochentwickelten
Mechanik kann die Drahtumdrehung
geändert werden, damit sie regelmäßiger
wird und für die Erfassung von Haupt- und
Streifenfarbe mit einem einzigen Sensor
eingesetzt werden kann.
Typische Anwendungen
und Prüfergebnisse der
Inline-Messung
Geprüft
wurden
verschiedene
Produktionseinstellungen
um
die
typischsten Anwendungen zu decken:
Die erste Prüfung mit einfarbigen Drähten
lag darin, das Ziel einer Auflösung von
mindestens
∆
E
≈
3 zu prüfen, um ein
Ergebnis zu erreichen, das der Prüfung
eines menschlichen Augen gleichen
würde oder besser wäre.
Bild 4
zeigt eine
detaillierte
graphische
yt-Darstellung
einer Messzeit von 15 Minuten für alle
3 L*a*b* Koordinaten eines gelben
Drahts.
Das
Histogramm-Maxima
(88/-66/39,25) entspricht durchaus den
durchschnittlichen
Werten
(87,62/-
66,04/39,10), die benutzt wurden, um
∆
E
entsprechend der Gleichung zu berechnen
(1). Wegen der oben genannten Jitter
und Oberflächenveränderung, ist der
FWHM-Wert des Luminanzkanals L* höher
als der der Kanäle der Reinfarbe a* und
b*. Das Histogramm aller
∆
E-Werte im
Bild 5
stellt ein Maximum von zirka 0,75
(Durchschnittswert 0,89) dar und ist ein
Beweis, dass das System eine Auflösung
von mindestens
∆
E=1 aufweist.
Keine Werte über 3 werden erfasst, daher
könnte eine Schwelle bei Werten von
5-7 für den Farbfehleralarm eingestellt
werden.
Durch
das
Einfügen
eines
Korns
von
Blau-Masterbatch
in
die
Schneckenaufgabe,
erhöht
sich
∆
E
wesentlich bis zu Werten ≥ 10 (Mitte von
Bild 6
) für 1-2 Minuten. Die geringere
Erhöhung von
∆
E zirka 3 Minuten später,
kann als Blaurückstände interpretiert
werden, die eine gewisse Zeit lang noch
irgendwo auf der Schnecke waren. Nur
der Hauptunterschied wurde später durch
eine Sichtprüfung erfasst.
Prüfung Streifenmangel (Extr.), rot-grau
Zeit (s)
a*/b* - Kanal [.]