
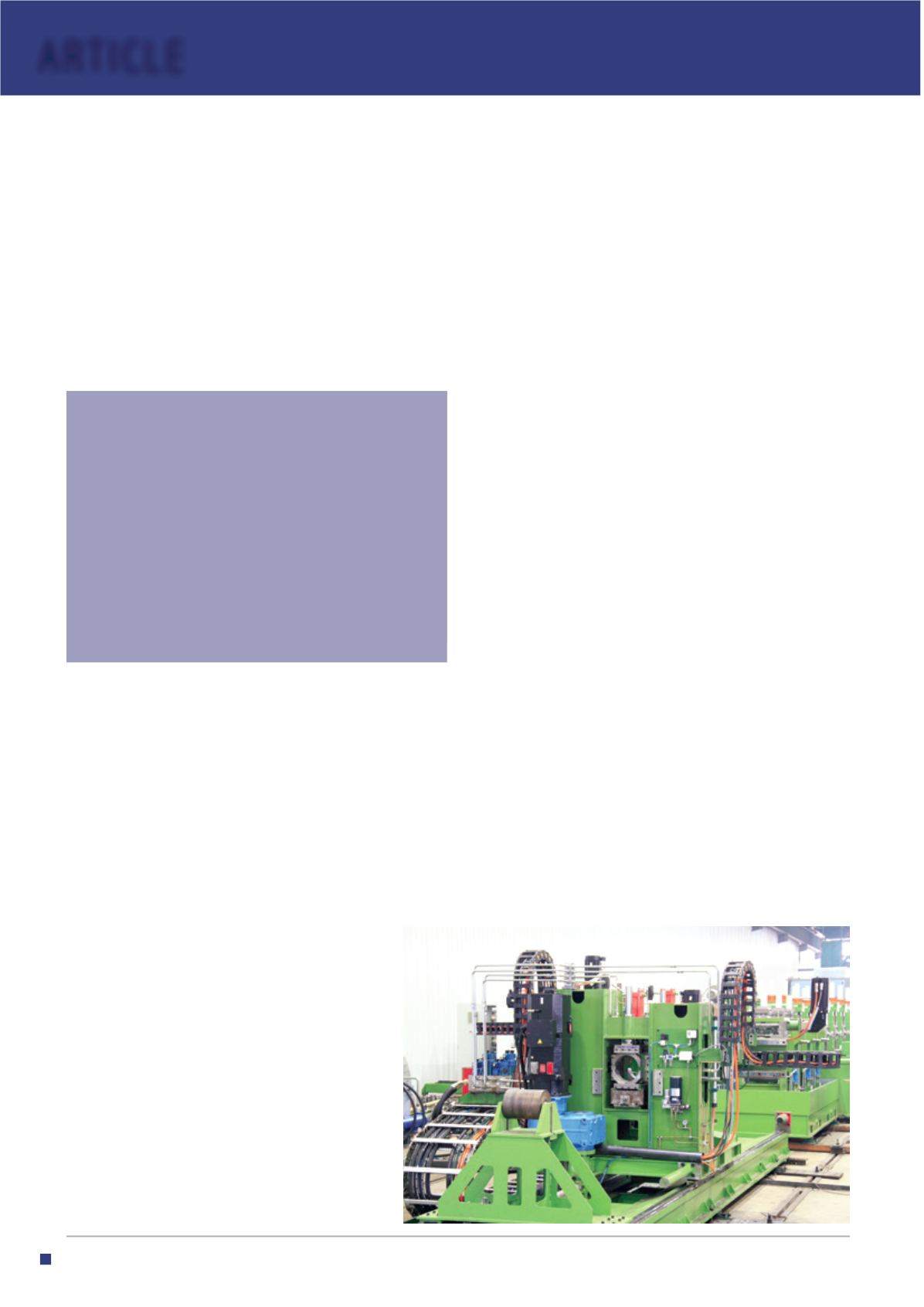
78
J
ULY
2016
AR T I C L E
Dalian Field
xx
Tube mill productivity and line speed
are equally impor tant for the market
competitiveness of a tube plant
By Guowu Gao, chief engineer at FD Machinery
It is correct in theory, but it is not the same in reality: the
highest quoted line speed is applied to the smallest tube
size only, and as the tube size grows the speed is lowered
dramatically. The more the speed falls, the lower the overall
productivity. So, high nominal speed does not always mean
low productivity and vice versa.
Specialists in tube machinery design know very well that line
speed depends on the following:
1) power capacity of the forming section
2) power capacity of the HF welder
3) power capacity of the flying saw (milling saw)
There are some other elements that influence the
line speed, such as entry section, pipe collecting
section, labour intensity and so on, and the most
important are the three mentioned above.
The power of the forming section can be increased by
strengthening the mill structure, and the HF welder
capacity can be increased by raising power output.
Also, the only item that influences the speed and
can not be upgraded is the cut-off (flying saw). The
cut-off is a real bottleneck that holds down the speed
limit of the entire mill. It is possible to determine the
possible line speed by the power capacity of an HF
welder; for example for a 76mm tube mill, as you
make a 76mm/4mm tube, the line speed with a
200kW welder will be 40m/min, and a 300kW welder
will give you a speed of 60m/min. For tube mills that
use a milling saw for cut-off, the choice of a 300kW
welder is a mistake, only because the performance
For a tube mill, line speed is a very important indicator.
Normally the line speed for small mills can be up to 120-
150m/min, middle mills up to 80-100m/min and large
mills up to 40-60m/min. But in daily factory conditions
tube mills seldom run at the highest speeds. In my 28
years of experience in tube machinery construction, I
have only once witnessed a Turkish company run their
line at 150m/min on regular basis. In a debate on what
the best choice of tube mill characteristics is, many say
that speed is most important, while others argue that
speed is not important at all. This is because the most
important characteristic of a tube mill is productivity. One
may say that speed just means productivity, because the
higher the speed the better the productivity.
of the cut-off will not meet the performance of the welder in
respect of speed. (There are some technologies for making
long tubes and cutting them for desired length offline, which
there is not enough room to discuss in this article.)
Both 200kW and 300kW welders for 76mm/4mm tube mill will
provide a “nominal” speed for this mill as fast as 120 or even
150m/min, as these high speeds are applicable only to smaller
sizes of tube that this tube mill is capable of producing; the
power of this welder is enough to provide enough speed for
small tube production.
As you start making tubes with larger gauge, it is clearly
seen that by raising the capacity of the welder from 200kW
to 300kW you can raise productivity by 30 per cent. While
making a tube with thinner wall, for example 76mm/1mm, the
speed can be up to 200m/min. But the recommendation from
the equipment producer will not exceed 100m/min, otherwise
the cost of the saw blades and the productivity loss due to line
stop for blade changes will greatly exceed all the benefits of
the speed, which of course no producer would want.
We have already mentioned that in the case of using a
300kW welder for 76mm/1mm tube production, theoretically
the line speed can reach 200m/min. If all other sections of
the line (forming, cut-off, entry, packing, etc) could meet
this speed requirement, this would be the line with the
highest productivity in the world, with three to four times the
productivity of an ordinary mill. We may also say that a line
with this high productivity saves three to four times on labour,
Two-blade milling saw