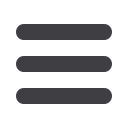

Technical article
July 2016
52
www.read-eurowire.comDesign Analysis of a Large
Planetary Strander using
CAE tools
By Giorgio Pirovano, MFL Group, and Fabiano Maggio, EnginSoft SpA
Introduction
The design of a stranding and closing
planetary machine with back-twist is not
a simple project, due to the “planetary”
rotation of the parts: that introduces
dynamic effects that are difficult to
estimate; in particular if the performance
is extreme due to large spool mass, load
configurations and rotation speed.
In order to avoid any possible risk and
to obtain the most precise design input,
MFL involves EnginSoft and its simulation
capabilities as reliable partner in this
project.
For this specific project, EnginSoft is
in charge of carrying out the whole
dynamical assessment of the planetary
machine. In order to achieve reliable
and precise results, it is necessary to
use a powerful and versatile multi-body
software: RecurDyn®.
On the other hand, MFL has to complete
the design of all parts in order to meet
structural requirement in terms of strength
and lifetime.
Methods and
problem definition
This colossal planetary machine will be
used to produce cable with different
diameters and strand combinations, so
that the spools loaded on the machine
can be different in size and position on
the main rotor. In addition, the spools
are naturally unbalanced due to winding
errors.
This results in various load scenarios to be
analysed. The goal is the identification of
the worst case in terms of power required
to the motors and stress on parts.
EnginSoft’s engineers are in charge of
finding out such worst conditions through
dynamic simulation.
The approach starts with a single cage,
and an analysis defines the worst
configuration. After that, together with
MFL, finite load scenarios are defined.
The next step is the dynamic simulation
of the different load scenarios by applying
the worst cage condition previously
defined. At the end it is possible to obtain
the worst working condition of the whole
machine.
In other words, this activity is the scientific
and precise application of the design of
experiment (DOE).
Rigid body
dynamics model
A rigid body dynamic analysis is
performed; internal loads and motor
power torques mainly depend on accele-
ration and inertias of moving parts, so that
there is not a clear need of introducing
flexibilities into the model (which would
significantly increase the computational
effort).
Starting from the MFL 3D CAD geometry
of the machine, the dynamic model is
defined in the RecurDyn® environment.
The result is an accurate model with more
than 100 bodies.
Most of the inertial proprieties are derived
automatically from CAD, but several
bodies are parametrised inside the
multi-body software.
Obviously, the connection between the
different bodies perfectly simulates the
real kinematic link (gear, shafts, and so on)
in order to obtain a model which is the
closest as possible to the real machine in
terms of degrees of freedom.
Gear elements are special features of the
RecurDyn® library, designed to simulate
both kinematics (transmission ratio) and
dynamics (reciprocal loading) occurring at
any gear couple.
Figure 4
shows the gears
back-twist system. It is easy to see that
the “gear feature” of RecurDyn® has been
massively used due to the conformation of
the transmission chain.
▲
▲
Figure 1
:
Rotations on a planetary stranding
machine
▼
▼
Figure 2
:
Single cage of planetary machine
▼
▼
Figure 3
:
Method and DOE approach
Single cage
Single cage
Single cage
Spool dimension
DOE
Load on parts
Motor’s
power
Spool
unbalance
Spool
combination