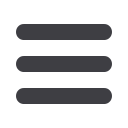

M
ay
2010
107
›
A
rticle
Tested and analysed models
In total, in experimental part, four experimental specimens were
tested after manufacturing. All specimens had similar geometric
properties such as 2.46m length, 10.2cm diameter and 0.25mm
thickness. Rings had 10.2cm inner diameter, and 12.2cm outer
diameter and 2mm thickness. The only difference between
specimens was the number of attached rings on specimen. For
identifying specimens they were labelled such A4. This label shows
that the specimen has geometric properties such was mentioned
elsewhere, with four ring stiffeners where two of them were end
rings and two others were middle rings. In fact, in each specimen,
rings had equal spacing.
In FEM analysis, all experimental specimens were exactly modelled
and analysed. Three other models were also analysed, which had
no corresponding experimental specimen, because of the difficulty
of manufacturing them experimentally. Two of them had four rings
such as model A4 but with different thickness. They were labelled
as A4 t20 that shows the model is a similar model A4 with four
rings but with 20mm thickness. These models were analysed for
comparing with model A4 to investigate the effect of the ring’s
thickness on behaviour of pipeline. Another model had no rings but
different thickness which labelled B0. This model had geometric
imperfections such model A0, and weight equal to model A13. This
model was analysed, for comparing two same weight models A13
and B0 with model A0 to investigate the economic benefits of using
of ring stiffeners. Geometric properties of models and specimens
and their labels are shown in table 1.
Experimental buckling and post
buckling modes
As is shown in table 1, in total four specimens were experimented
with, buckling behaviour of specimens are shown in figures 6, 7,
8, 9, 10 and 11. In these figures behaviour of specimens are about
axial, circumferential-pressure strains and radial displacement-
pressure.
Figures 6 and 7 are about axial strain of specimens. Figure 6 shows
axial strain-pressure curve of specimen A0 as basic specimen. Initial
buckling of test occurred at 6.0 Kpa. Figure 7 shows comparisons
between specimens A4, A7 and A13 with the buckling pressure 17.0
Kpa, 27.8 Kpa and 61.9 Kpa respectively. When comparing figures
Study
type
Label
Rings
number
Length
(m)
L
Diameter
(m)
D
Thickness
(mm)
t
Rings
spacing (m)
L
c
Rings inner
radius (m)
Rings outer
radius (m)
Rings
thickness
(mm)
EXP
A0
0
2.46
0.102
0.25
-
-
-
-
A4
4
2.46
0.102
0.25
0.82
0.102
0.122
2
A7
7
2.46
0.102
0.25
0.41
0.102
0.122
2
A13
13
2.46
0.102
0.25
0.205
0.102
0.122
2
FEM
A0
0
2.46
0.102
0.25
-
-
-
-
A4
4
2.46
0.102
0.25
0.82
0.102
0.122
2
A7
7
2.46
0.102
0.25
0.41
0.102
0.122
2
A13
13
2.46
0.102
0.25
0.205
0.102
0.122
2
A4 t20
4
2.46
0.102
0.25
0.82
0.102
0.122
20
A4 t0.25
4
2.46
0.102
0.25
0.82
0.102
0.122
0.25
B0
0
2.46
0.102
0.3625
-
-
-
-
6 and 7, differences between initial buckling of specimens and their
behaviour are identified (table 2). When comparing the curves it is
clearly indicated that a specimen
’
s buckling pressure was increased
when rings spacing decreased.
At this point, firstly initial buckling was started in a small part
of specimens in circumferential and longitudinal direction of
specimens, then buckling propagation gradually started on post-
buckling region.
With test continuing, inner pressure of specimens reduced. In
fact, increasing value of buckling pressure intensively related with
2L
c
/D
.
Table 1
:
Geometry of test models and specimens
Figure 6
:
Axial strain-pressure curve of specimen A0
Figure 7
:
Comparison of axial strain-pressure curves of specimens A4, A7 and A13