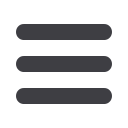

108
M
ay
2010
www.read-tpt.com›
A
rticle
Figures 8 and 9 show circumferential strain-pressure curves of
specimen A0 and comparing between specimens A4, A7 and A13,
respectively. Nonlinear elastic behaviour before occurrence of initial
buckling is visible in curves, clearly. In Figures 10 and 11 the radial
deformation of specimen A4 and comparing between three other
specimens in experimental study are plotted in some selected
nodes of pipe wall.
FEM buckling and post buckling modes
Figures 12 and 13 show radial deformation of models in FEM
analysis study. Figure 12 shows radial deformation-pressure curve
of model A0 with 7.1 Kpa and 18% difference with experimental
result. Figure 13 shows this character for models A4, A7 and A13
with 18.1 Kpa, 32.4 Kpa and 49.8 Kpa which have 6%, 16.5% and
24% differences with experimental results (table 2).
When comparing experimental and FEM curves, some differences
are shown, such as value of initial buckling pressure or post-
buckling part of curves which occurred with pressure decreasing in
the experimental study and with the constant load carrying capacity
in the FEM study. This is because of some problems such as
unabling in modelling residual stress.
As mentioned above, additionally, two models were analysed in
terms of investigating the effect of rings thickness on the behaviour
of pipeline. These models are compared with model A4. Models A4
t20 and A4 t0.25 had four rings with 20mm and 0.25mm thickness
respectively while the basic model (A4) had 2mm thickness. Model
A4 t20 was 26.05Kpa and model A4 t0.25 with 18.8 Kpa initial
Figure 9
:
Comparison of circumferential strain-pressure curves of specimens A4,
A7 and A13
Figure 8
:
Circumferential strain-pressure curve of specimen A0
Figure 11
:
Comparison of radial displacement-pressure curves of specimens A4,
A7 and A13
Figure 10
:
Radial deformation-pressure curve of specimen A0
Figure 13
:
Comparison of radial displacement-pressure curves of models A4, A7
and A13
Figure 12
:
Radial deformation-pressure curve of model A0