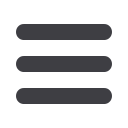

M
ay
2010
109
›
A
rticle
buckling pressure with 43% and 3.8% differences to the basic model
(table 3). As indicated, deceasing or increasing the ring thickness
does not have a great effect on pipeline behaviour against the
amount of steel that is used in rings. It is so economical that as
thickness of rings decreased if it will be enforceable. These curves
are shown in figure 14.
Figure 14
:
Comparison of radial deformation-pressure between models A4 t0.25
and A4 t20
Model label
Buckling pressure
(Kpa)
Difference between
basic specimen (%)
A4, basic model
18.1
0%
A4 t0.25
18.8
3.8%
A4 t20
26.05
43%
Table 3
:
Comparison between models A4, A4 t0.25 and A4 t20
In addition, another model was analysed without rings, but with
more thickness and the same weight was used with the model.
This model was for investigating the economical aims of the study.
As indicated in figure 15 initial buckling of this model is 20.5 Kpa
and the pressure ratio of the basic model (A0) was equal to 2.88
whereas this ratio for model A13, with the same weight model
B0, was 7.01 (table 4). This shows the economical benefits of
decreasing the amount of steel used.
Specimen label
Experimental buckling pressure (Kpa),
pressure ratio with basic specimen (A0)
FEM analysis buckling pressure (Kpa),
Difference with basic specimen (%)
Differences between experimental
and FEM study (%)
A0, Basic specimen
6, 1
7.1, 1
18%
A4
17, 2.83
18.1, 2.54
6%
A7
27.8, 4.63
32.4, 4.56
16.5%
A13
61.9, 10.31
49.8, 7.01
24%
Table 2
:
Comparison between experimental and FEM studies results
Model label
Buckling pressure
(Kpa)
Difference between
basic specimen (%)
A4, basic model
7.1
1
A13
49.8
7.01
B0
20.5
2.88
Table 4
:
Comparison between models A13, B0
Circumferential buckling mode
Another observation in experimental and FEM studies, was made
to do with circumferential waves on wall of specimens and models
which identified with n and strongly depend on geometric ratios of
D/2
t
and
D/2L
c
. The higher ratios have higher number of n and
therefore higher value of buckling pressure. There were some
differences in this case between two studies, such as the made-up
waves number on the specimen panels in experimental study were
different but these values were constant in the FEM study (table 5).
As shown, initial buckling of specimens was increased by increasing
the number of circumferential modes of specimens. Figures 16, 17,
18 and 19 indicate the number of waves which were used on panels
of specimens.
Figure 15
:
Radial deformation-pressure curve of model B0
Figure 16
:
Three and two
made-up wave
mode on panels
of specimen A4 in
experimental study