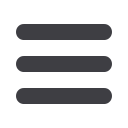

EuroWire – July 2009
54
Wire products for the automotive industry
Automotive U-bolts
Since 1973 Videx Machine Engineering has manufactured machinery for U-bolts and other bent parts for the automotive industry,
working directly from wire coil. Two years ago, Videx introduced a new bending system with a slide bending die and an integral
stripper mechanism.
With this new line, the VAS-DBQ range of machines, users no longer need to make bending dies for each part: the machines are
supplied with a floating bending die, that covers the entire range of round and square bottom U-bolts, enabling new sizes of U-bolts
to be made in minutes.
VAS-DBQ models are equipped with a positive stripper system that
allows the machines to run at maximum speed without the risk of
jammed parts.
The VAS machines pull wire from coil, straighten, cut to length,
chamfer and thread both ends and bend to shape. They can also
perform cold forming operations, such as heading and extrusion, and
material removing operations such as drilling and pointing. Chamfer
cutting or rolling, thread or form rolling, knurling, collaring, grooving
and flattening are among the other operations that can be performed
by the machines in any sequence.
▲
▲
A chamfered U-bolt made on a Videx machine
Videx Ltd – Israel
Fax
: +972 3536 4802
:
videx@videx.co.ilWebsite
:
www.videx.co.ilSprings for interiors
In a modern car interior there are springs in the centre console, glove box, cup holders, grab handles, sun visors and door mechanisms,
all with different characteristics to be taken into account, with such factors as tactility and strength, available space and operational life.
William Hughes offers a design service to engineer individual springs that provide the most cost effective solution for each purpose.
Torsion springs provide a perfect solution for many automotive applications. They can be either single, which gives a higher force in
a smaller space, or double, which provides a balanced force or torque. To overcome friction, a problem in some applications, springs
can be coated with special materials or the spring geometry
can be optimised to minimise the effect. Other options
include tension or compression springs in a range of sizes
and materials.
In modern vehicles, each part of the car interior needs to
impart the right ‘feel’ to the driver. When design engineers
at William Hughes were asked to develop a special torsion
spring to release an armrest catch on a central console,
ergonomics were the primary consideration. The catch
mechanism had to be designed to slow the movement of
the console to make it open gently; it also needed to be
easy to operate with minimum effort.
The team at William Hughes was provided with a complete
set of parameters for the operation. In order to provide
the best solution, the design engineer needed to fully
understand every aspect of the application to ensure that
the proposed design would be both economical and fully
compatible with the plastics and fabrics also used in the
assembly. The designer needed to consider how the unit
could be assembled quickly and easily.
With the help of the latest computer aided design software and specialised spring data, William Hughes used knowledge and
experience to develop a spring that was optimised for the application. In this instance a single torsion spring provided the best
solution and William Hughes was able to quickly produce prototype springs for evaluation before the design was finalised for volume
production. In addition to special springs for car interiors, William Hughes can also manufacture a wide range of bent wire forms and
sub assemblies for car seats and trim panels.
William Hughes Ltd – UK Fax
: +44 1963 363640
:
sales@wmhughes.co.ukWebsite
:
www.wmhughes.co.uk▲
▲
Single and double torsion springs from William Hughes will be found in many car
interiors
s